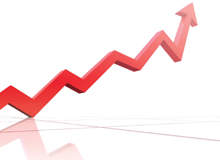
Quality has emerged as an elusive differentiator in medical device manufacturing. Increasingly complex production environments, company mergers, and the use of international supply sources are causing quality problems in the medical device sector to escalate.
The most serious consequence of poor quality, in terms of safety and financial impact, are recalls. In the US, Food and Drug Administration (FDA) device recalls for 2008 were at an all-time high, with 845 individual medical device recalls, which was more than double that of 1998’s figure of 358.
While there are more devices available now than there were in 1998 and the devices are more complex, this is still an alarming trend (Figure 1).
It is also alarming that there were 17 FDA Class I recalls during 2008. An FDA recall is listed as Class I when there is a reasonable probability that the use of or exposure to the product will cause serious health consequences or death. Typical Class I recall issues for 2008 included:
- Battery caps used with insulin pumps and glucose monitoring systems exhibited intermittent power loss due to loss of contact between the battery cap and the battery canister, which resulted in the device resetting.
- An infusion pump motor stalled due to gear shaft wear.
- Inaccurate flow rate in a pump module due to misassembled (missing, bent or broken) springs.
- Packages of insulin syringes were labelled for use with U-100 insulin, but actually contained a syringe designed for use with U-40 insulin.
- An automated external defibrillator was configured with the wrong software.
- Stents suffered from detachment of the tip from the delivery system.
- A cranial implant kit was recalled due to lack of assurance of sterility.
The data presented here is from the US FDA, but the device quality stated is an international issue. A typical manufacturer will now purchase components or raw materials from several countries to produce a product that will be sold in numerous other nations around the world.
Almost every nation or group of nations has some type of governing body in place to regulate manufacturers and import/export activities. For example, the EU has a central law called the Medical Devices Directive that is honoured by all member states. Each nation within the EU also has its own equivalent to the FDA that regulates products.
Although these systems vary, they serve the same purpose so there are many commonalities. Many nations also recognise the ISO-13485:2003 standard as basic requirements for a management system for the design and manufacture of medical device products.
A large portion of ISO-13485:2003 is dedicated to the monitoring and measuring of processes requirements. The standard states that not only must the organisation establish and implement methods of monitoring and measuring processes, but it must also demonstrate the ability of the process to achieve planned results. Additionally, the organisation must maintain corrective actions to ensure achievement of results.
Regardless of what regulatory system or standard we are trying to meet, if the goal is to reduce the risk of producing defective products, then it is best to follow the advice of ISO-13485:2003 and monitor the process. The only way to truly monitor a process is to understand its behaviour within normal statistical boundaries. Improving the process follows naturally when these statistical anomalies are identified.
The need to understand the process’s behaviour points directly to statistical process control (SPC). Use of SPC will allow us to understand what is normal for our process and to immediately be aware when the process deviates from that normal state.
What is statistical process control?
SPC is a method of controlling and improving a process through the use of measurements or data. SPC data is collected in real time during the manufacturing process, and SPC monitors the process itself, so that variation that may affect the final product is detected and corrected during production. SPC has a major advantage in that it is preventive while other methods are reactive and focus on problems detected in the end product. SPC data may be either measured values (variable), or counts of defects or defective items (attribute), making it applicable to virtually any manufacturing or service process.
SPC data is plotted on a control chart and control limits are determined based on the capability of the process. These control limits define the normal behaviour or common cause variation of the process. If the process data is within the control limit then we know that the process is operating as we would expect it to. As long as the process data is within these limits, there should be no adjustments or changes made to the process.
If we adjust a process that is in control or has all process data within the control limits, then we are tampering with the process. Tampering with a process that is in control will increase variation and the risk of producing defective products. Data that falls outside of the control limits indicates that the process has changed and that an assignable cause has created the increase in variation. When an assignable cause occurs, it should be evaluated and action must be taken to correct it, as shown in Figure 2.
American statistician W Edwards Deming once said that “You cannot inspect quality into a product; it is already there”. SPC gives the knowledge to build in the quality by giving us the tools to implement adequate record keeping and detect issues earlier.
Application of SPC not only stabilises the process by allowing it to perform on target at its capability, but it also highlights assignable cause variation, which may be eliminated to improve the process. Using SPC will dramatically reduce variation within the process, leading to less waste and rework. Productivity is greatly improved since decisions are made in real time on the shop floor instead of after the production has been completed. Another benefit is that the charting of key characteristics will also uncover hidden process personalities, which often point to machine abnormalities, issues with raw materials, or even operator training.
Software in the medical device environment
Any SPC software system evaluated must first be capable of collecting real-time process data and presenting it to the user in a statistically valid, easy-to-understand control chart. The software should also include analytical tools that allow you to perform comparative analysis to uncover hidden effect relationships that can lead to further process improvement.
However, when implementing an SPC software system in a medical device environment, consider that the system must comply with any governing regulatory bodies. Regardless of whether the goal is to meet CFR Part 11, ISO-13485:2003, or a national regulatory system, the SPC system should include the following basic requirements:
- A security policy that allows configuration of the user password. This should allow control of items such as password age, password length and format, and whether passwords may be recycled.
- The SPC software’s database should maintain an access log for traceability of system usage and log-in or access violations.
- The SPC software’s database should include audit tables that capture any editing or deleting of any record or field in the database. These audit records should be easily viewed, but not editable.
- The ability to force users to enter reason for change. Change history and reason for change reporting should be available for any chart printout.
- Include electronic signatures as required for data entry, data editing, changing of limits and entering comments.
- The ability to ‘lock’ data used for customer reports to ensure that the data is not tampered with after the report is issued. For example, data that was included in a lot summary report cannot be edited without forcing the user to recreate the lot summary report.
- Validation scripts to guide the user through the software validation process. Ideally, the SPC software company should be able to provide validation support.
- The option to require the user to input assignable cause codes and corrective action codes whenever process events are recorded.
In addition to having the proper security, auditing and tracking features, and real-time SPC control charts, an ideal system will also ensure compliance with your sampling strategy. The world’s greatest SPC system is of little use if the data isn’t being collected properly or if there is no proof that the inspections were completed.
Software incorporating a sampling scheduler and sampling compliance reporting is a major asset when striving to meet regulatory requirements. The sampling scheduler should prompt the operator at the correct measurement time based on the state of the process. The sampling scheduler should also be able to notify others and take action if the sampling requirements are not met.
This feature should also include a sampling compliance report that includes how many samples were required within a specific range, how many were actually measured, and sampling percentage along with other basic information such as the process state, part and machine information.
As an example, if the process is running in a normal state, the operator may be prompted to sample every 30 minutes; if the process is in an enhanced sampling state, the operator may be prompted to sample every 15 minutes (Figure 3). Whenever the process is idle or stopped, sampling should not be required and a record of the stoppage should be recorded.
Other features that may be found in the SPC software include: lot genealogy to assist with tracking of component lots within finished products, event monitoring systems that give the ability to take action when process events occur, such as email notification or even stopping a process, and also acceptance sampling capabilities to evaluate incoming materials or components.
The role of the company
Equally as important when evaluating SPC software is the software company itself. Is the company stable and profitable? Where are they ranked within the SPC software industry? Are they continuing to develop the product? Do they employ technical experts, statisticians and a knowledgeable technical support staff ready to assist you? While hundreds of SPC software programmes can create control charts, there are very few that give you access to the resources to create a world-class process control system.