
Researchers at the Harvard John A Paulson School of Engineering and Applied Sciences (SEAS) and the Wyss Institute for Biologically Inspired Engineering in the US have developed a new approach to generate robotic actuators with integrated sensing capabilities.
With the new manufacturing platform, the soft robots will be able to sense movement, pressure, touch, as well as temperature.
To address the concerns with existing rigid electronics, the team created a conductive ink that is based on organic ionic liquid and can easily be 3D-printed within the soft elastomer matrices used in the majority of robotic actuators.
The researchers adopted an established method called embedded 3D printing designed for fast and optimised incorporation of different features and materials in a single soft body.
Combination of this method and the new ink is intended to fuse soft sensing and actuation within one integrated soft robotic system.
SEAS former postdoctoral fellow and researcher Michael Wehner said: “To date, most integrated sensor / actuator systems used in soft robotics have been quite rudimentary.
How well do you really know your competitors?
Access the most comprehensive Company Profiles on the market, powered by GlobalData. Save hours of research. Gain competitive edge.
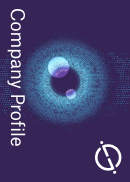
Thank you!
Your download email will arrive shortly
Not ready to buy yet? Download a free sample
We are confident about the unique quality of our Company Profiles. However, we want you to make the most beneficial decision for your business, so we offer a free sample that you can download by submitting the below form
By GlobalData“By directly printing ionic liquid sensors within these soft systems, we open new avenues to device design and fabrication that will ultimately allow true closed-loop control of soft robots.”
The researchers tested the sensors by printing a soft robotic gripper with three soft fingers and embedded with various contact sensors. It was then explored for the ability to sense inflation pressure, curvature, contact and temperature.
Over the coming months, the team plans to train the new devices using machine learning to grasp objects of different size, shape, surface texture, and temperature.