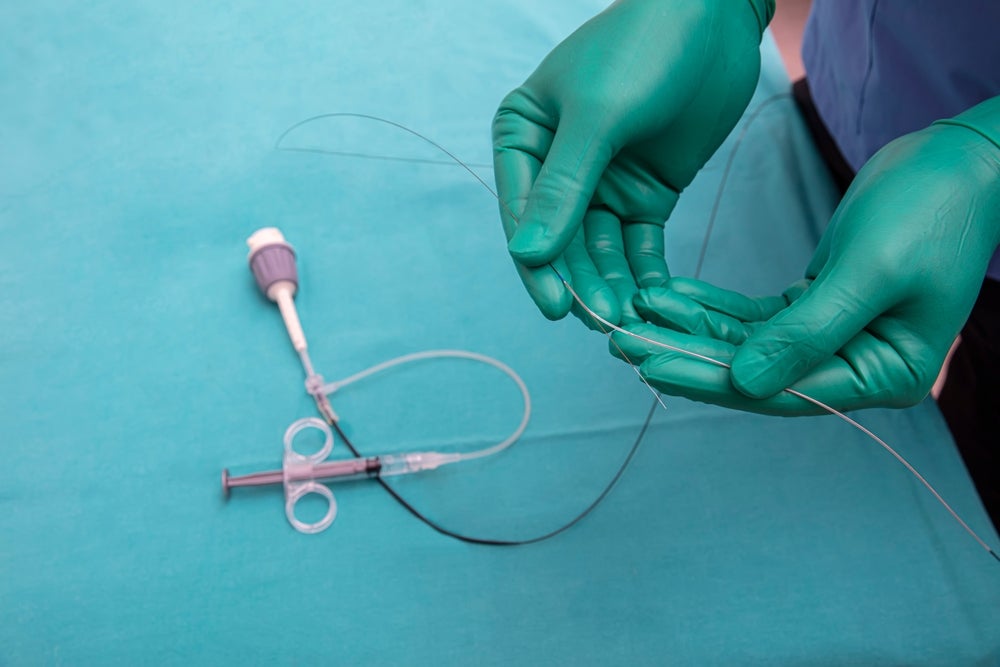
Precision medicine and less invasive treatments are gaining importance in the quickly evolving healthcare business and the medical device industry is continuously innovating to create smarter devices for better patient outcomes and shorter hospital stays.
With in-vitro diagnostics and cardiovascular devices projected to be the biggest medical device markets this year, according to a Thematic Intelligence report by GlobalData, more developments are expected in the field of guidewires, which will make complex medical procedures safer and easier for patients and healthcare professionals.
Guidewires are an integral part of minimally invasive surgeries that reduce surgical trauma and accelerate recovery. These flexible wires are crucial medical tools that pass through the body’s pathways, allowing access for a larger device such as a catheter to reach a specific part of the cardiovascular system.
Enabling smart-wire solutions
While super-elastic nitinol and 300 series stainless steel are frequently the top choices for guidewire manufacturers, experimentation is an important component of innovation. The choice of coating, which can be hydrophilic or non-hydrophilic, is also key.
“Deciding which guidewire to use depends on several factors, such as indication or lesion of interest, the torque and lubricity of the wire,” says Joselia Carlos, medical device analyst at GlobalData.
“Something physicians keep in mind when making this decision is that non-hydrophilic wires have more friction but provide better tactile feedback, while hydrophilic wires offer less friction and are easier to guide.”
Exploring unique combinations can assist manufacturers in selecting the ideal design for their businesses.
“During the design phase of new guidewires, engineers are often trying to merge the advantages of different materials. For example, they might look to achieve the stiffness of stainless steel, but also the flexibility of nitinol,” says Jim Boldig, director of sales and engineering at Custom Wire Technologies (CWT), a leading provider of custom-designed medical wire components, including guidewires.
Coronary market is leading the way
The recent US Food and Drug Administration-approved FreedomFlow® Peripheral Guidewire by Cardio Flow is the latest offering in the peripheral guidewire market.
The adaptable wire features a stainless-steel core-to-tip design with a fixed distal-spring coil. It has a silicone-coated spring coil and a silicone coating on the distal 200cm. It has proven effective in the endovascular lab, efficiently navigating blockages and delivering multiple interventional devices on a single guidewire.
Carlos believes the coronary guidewire market is witnessing more innovation than that for peripheral guidewires, saying: “Improvements in technology ensure a strong entry in this market. For example, Soundbite’s Crossing System is the first guidewire to provide a simpler and more clinically efficient method for treating chronic total occlusions.”
A further innovation in this area is Cardiovascular Systems’ ViperWire Advance® with Flex Tip, the first and only nitinol atherectomy guidewire. With its flexible nitinol core and malleable tip, the device is better suited for navigating complex anatomy, while its flexible nitinol body helps to reduce wire bias during atherectomy.
How customisation can foster innovation
Novel designs can necessitate the use of altered grinding and coiling techniques. Boldig explains: “With advancements in new materials, the standard practices for grinding stainless steel or nitinol do not apply. As a technician sets up a machine, something that works well for stainless steel or nitinol will rarely work for new material. Extra effort must be applied to allow these new materials to grind with the same precision and quality that customers have come to expect.
“One of our raw material suppliers has developed a proprietary product that is able to merge the two materials together into one solid wire. Our grinding department can remove the outer layer of stainless steel to expose the inner layer of nitinol.
“This will give the wire proximal stiffness and distal flexibility. The material, combined with our grinding experience, can provide the engineers with a unique design that very few products on the market possess.”
Smaller and smaller
Boldig hints that CWT is currently working on two new products for cardiovascular and neurovascular purposes.
“CWT is developing the complete manufacturing processes for these wires. Part of this development is the iterative process where we produce multiple designs of the ground wire for the customer to evaluate differences to narrow to a specific construction,” he explains.
“This could be a change in diameter or length for distal flexibility. It could be a variety of materials to see how they perform when the grinding remains the same. Our ability to react quickly helps the projects move along.”
Reducing equipment size is an essential part of medical device innovation to facilitate precise surgical procedures, and this trend of miniaturisation has trickled down to the world of guidewires.
“As engineers continue to push the scale of how small they wish to make their devices, we must compensate in our grinding process as well. It creates challenges for tolerance holding and tooling lifespan,” says Boldig.
“CWT creates prototype tooling [that will] be successful in these small, grinding processes. If we are successful with the one-off prototype tooling, it is also challenging to find a vendor who can make it in a production setting.”
Enabling next-gen guidewires
It is crucial for businesses in this sector to partner experienced medical component manufacturers to continue developing more advanced products. A company such as CWT, which has 20 years of experience in the industry, can work with clients to develop and produce customised guidewires using the latest technology and materials.
“Demand for grinding has remained consistent since 2021 and will into 2024. CWT has continued to invest in additional equipment to add capacity. This capacity has already been filled by new and existing customers,” says Boldig.
“We have been fortunate to hold our lead times. There are scenarios where we can deliver products ahead of schedule when machine openings happen. CWT has one more machine to receive in 2023, which will make eight in total in our grinding department.
“We are anxious to see what demands are in place for 2024 and how we can expand the department further,” he adds.
To learn how CWT can customise guidewire solutions specifically for your business, download the whitepaper below.