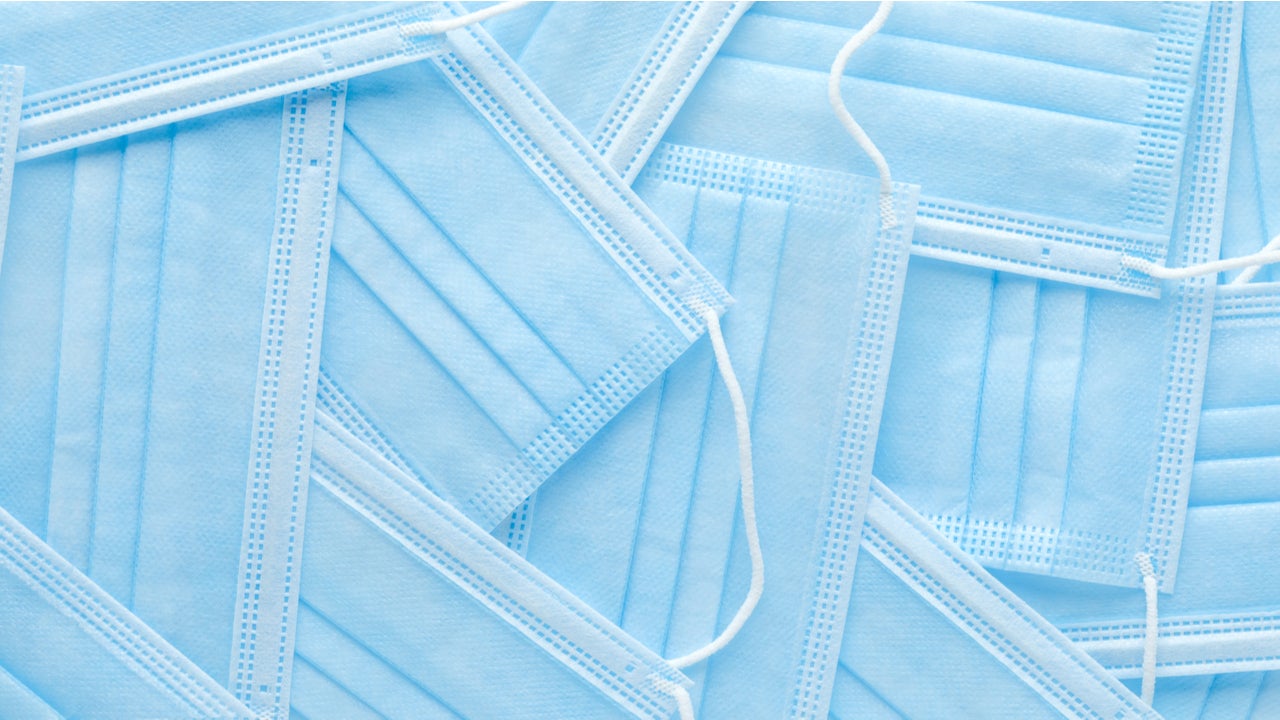
At the start of the coronavirus crisis, it soon became clear that personal protective equipment (PPE) was going to be a problem. Medics warned that there simply weren’t enough masks, gloves and gowns to protect them as cases of Covid-19 surged.
A BBC investigation in April 2020 found the UK Government failed to buy sufficient protective equipment to cope with a pandemic, which came as no surprise to frontline healthcare professionals and social care workers.
“The government is forcing doctors to place themselves and their patients in grave danger by expecting them to treat Covid-19 patients without adequate PPE,” said doctors’ union the British Medical Association at the time.
Covid-19 exposed the fragility of the healthcare supply chain. As SARS-CoV-2 snowballed around the world and global demand for PPE soared, the usual way of doing things stopped working. China, the largest producer of PPE, reduced its exports when the coronavirus was first detected in the region at the start of 2020.
Many other countries also imposed export restrictions on masks and respirators in the following weeks when it became clear that the coronavirus was taking hold globally. A desperate scramble for PPE ensued.
Risk calculation
Finding reliable suppliers in a crisis would prove difficult for healthcare procurement teams, partly because they don’t always have up-to-date information about a company’s risk.
How well do you really know your competitors?
Access the most comprehensive Company Profiles on the market, powered by GlobalData. Save hours of research. Gain competitive edge.
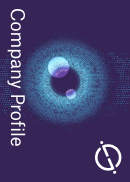
Thank you!
Your download email will arrive shortly
Not ready to buy yet? Download a free sample
We are confident about the unique quality of our Company Profiles. However, we want you to make the most beneficial decision for your business, so we offer a free sample that you can download by submitting the below form
By GlobalData“We didn’t need to do a lot of risk management or get risk alerts about what’s going on out in the country of manufacture,” Peter Smith, a former government head of procurement, told the Financial Times in May 2020. Covid-19 was a wake-up call.
A more responsive platform would help the NHS procure PPE from low-risk suppliers and prevent future shortages should another health emergency rear its head, say text mining experts at the University of Sheffield.
They are working with data science company Vamstar on a project that aims to help the NHS manage its supply chain more efficiently. The university-industry team is developing a tool that will automatically analyse procurement data from previous supply contracts.
It says the approach could help buyers rapidly evaluate the credibility and capability of potential suppliers to secure against shortages and low-quality products.
“This is a problem that is pervasive in the healthcare industry,” says Praful Mehta, Vamstar’s CEO. “In Western countries, you can buy an iPhone and it would be delivered tomorrow but your healthcare system is broken if it can’t even source facemasks.”
He explains that it’s possible to calculate a supplier’s risk from the goods and services they supply, the quality of the products and the company’s history of working with health services.
But manually working through reams of information from multiple sources is challenging and time-consuming.
A challenge eased with NLPs
Natural language processing (NLP) methods that extract and make sense of this historic data could transform the procurement process, says Ziqi Zhang, leader of the Sheffield team. “NLP involves automated methods to process a large amount of textual data into a structured format that a machine can understand,” he explains.
Computers would do the hard work and generate a risk rating for potential suppliers so the procurement team could make a more informed decision when choosing who to purchase healthcare products and services from. Zhang’s Sheffield team will work with Vamstar to incorporate their NLPs into a healthcare procurement digital marketplace.
Another possible contributor to the UK’s PPE problem was an over-reliance on just a few suppliers. When stocks from the health service’s trusted companies ran dry in 2020, procurement teams had nowhere else to turn.
This is despite reports of several small and medium-sized companies offering to help the government procure PPE who claim they were ignored at the time. Moving away from a manual procurement system could create opportunities for small and medium suppliers who may have previously been overlooked due to high barriers of entry.
“Efficient supplier sourcing, supplier selection and continuous supplier-risk assessment are the most critical tasks for any healthcare buyer,” says Vamstar’s chief technology officer Richard Freeman.
But currently, he says, many high-quality medical companies struggle to find buyers for their products and services due to health services’ cumbersome procurement processes.
Last year 44% of healthcare contracts within the EU received just one applicant and 15% had no bidders at all. Instant access to supplier data and risk profiles would make it easier for the NHS to access a wider supplier market, Freeman says.
Vamstar’s ultimate vision encompasses more than just PPE. It wants to build the world’s largest supply chain network, which will connect suppliers and buyers across the healthcare and life sciences industries.
It is also collaborating with public procurement experts from the University of Nottingham, such as Aris Georgopoulos, to help healthcare services better manage supply chain risks during emergencies. “In the future, a crisis like this should not impact the healthcare system’s ability to treat people,” concludes Mehta.