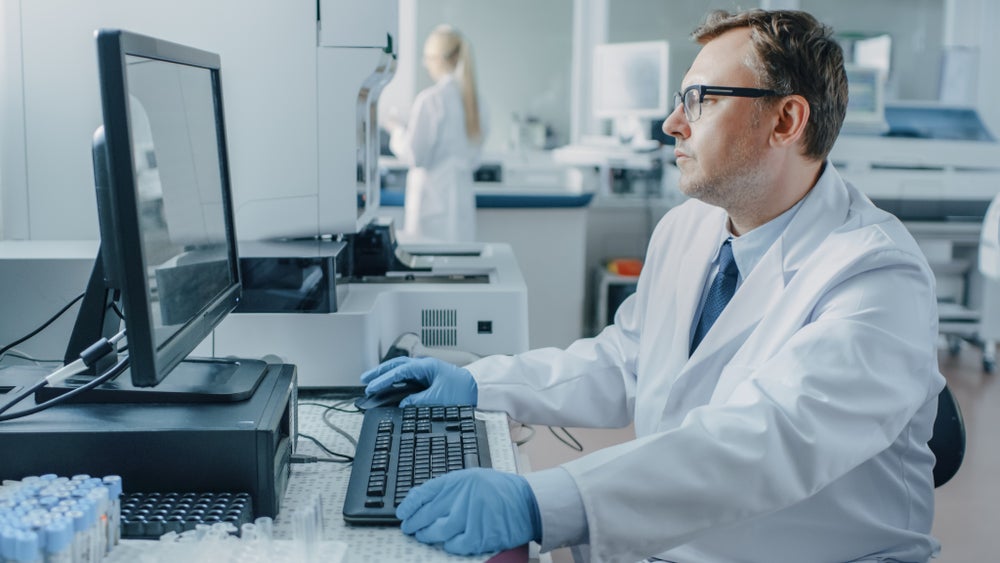
As timelines for medical device development get tighter and tighter, the bar is rising for supply chains. Working with suppliers who understand your need to deliver high-performance solutions within short timelines should be a top priority for manufacturers that want to stay competitive under the pressures of today’s industry.
Earlier this year, leading wire component supplier Custom Wire Technologies (CWT) revealed its new QuikCoil programme. Designed to provide fast turnarounds on custom coiling orders for R&D engineering departments, the programme guarantees deliveries within a week. Medical Device Network spoke to the company to find out more about the recent launch.
Lead times for catheter components
“Most component companies have expedited programmes where they can cut their lead time in half,” explains John Corsten, sales manager at Custom Wire Technologies. “This is because when R&D departments want to do prototyping, they want to do rapid prototyping. They need the components fast.”
Providing reinforcement coils for catheters has been a big part of CWT’s business since day one. Out of all the components of a catheter, coils have traditionally taken the longest amount of time to acquire. According to Corsten, most coil companies would have a three to four week (or more) lead time for custom products. By contrast, most other catheter components can be bought or made in one to two weeks.
Process mandrels, for example, are in stock up to sizes .150in, while mandrel sizes above that take two to three weeks to be custom made. Components such as PTFE liners, process heat-shrink, and marker bands are also in stock. In addition, many catheter companies have in-house extrusion capabilities and can produce their own outer jacket extrusions within a week.
When it comes to the metal component of a catheter, there are a few different options. These include braids, coils, helical hollow strain (HHS), and hypotubes. “Most catheter companies have in-house braiding which enables them to make braids in a week,” says Corsten. “Hypotubes are in stock so you can get one pretty quickly. Right now, the lead time for HHS stands at about five weeks but it will eventually come back down to two weeks. Everything is either in stock or available pretty quickly, except from the coil.”
For catheter manufacturers, longer lead times on coils are less than ideal. During R&D processes, engineers want to iterate designs quickly. They may have all the components they need but want to make a design change to only the coil or braid. To avoid delays and ensure smooth running in the R&D process, the need for a coil supplier who can offer fast turnarounds on orders is very clear. According to Corsten: “This is what gave life to the QuikCoil idea.”
Custom-made coils within a week
But it’s not just about speed, says Bob Boldig, president of CWT. “QuikCoil is a customisable R&D solution. It’s not just a boilerplate standard coil; the customer can specify exactly what they’re looking for.”
To design the right coil for the job, CWT will request details for the coil outside diameter (OD), inside diameter, wire OD, coil length, coil gap/spacing, and coil pitch. “The customer just needs to plug in the figures and then we will supply them with a fully customised coil,” says Corsten.
CWT has stock material for its QuikCoil programme, meaning the guaranteed one-week lead time only applies if the material is in stock. However, the company also invites customers to inquire about additional material availability and sizes, as there may be options available for use that are not listed.
In a post-pandemic world where lead times on a range of components and materials have been badly impacted, CWT’s dedication to keeping its customers R&D projects running on track further proves the company’s status as an important partner to the medical device industry.