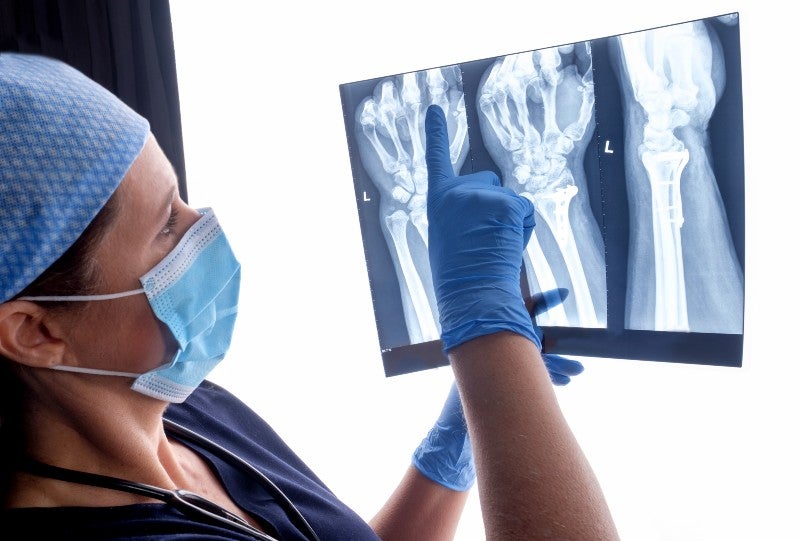
First introduced by Martin Kirschner in 1909, the Kirschner-wire (frequently shortened to K-wire) is an indispensable medical tool used extensively in orthopaedic surgery. Typically made from stainless steel due to the material’s strength and biocompatibility, K-wires are stiff, straight wires with a sharpened tip on one or both ends.
Also known as stabilisation pins, K-wires are inserted percutaneously (via the skin) to hold bone fragments together while fractures heal. They are generally removed after about three or four weeks, though in some applications K-wires can be inserted definitively rather than temporarily.
K-wires have become a standard of care for the treatment of metacarpal hand fractures, as well as other indications such as wrist, elbow, foot, and ankle fractures. Such injuries are common, and while fractured bones often do heal without intervention, orthopaedic surgery is frequently required. According to one report, there were approximately 22.3 million orthopaedic surgeries performed around the world in 2019.
A short wire with a long history
Like most long-standing devices of the medical industry, the K-wire has changed a lot since its original inception. While the earliest use of these pins was in skeletal traction for longer bones, today the K-wire is recommended for the fixation of smaller bones. The wire itself has become much smaller in diameter over its 100-plus years of use, reducing the incidence of pin-tract infections (PTIs) – a common side effect of orthopaedic surgery.
The methods used to insert K-wires have also evolved and remain a topic of discussion to this day. In the initial surgeries of the early 1900s, K-wires were hammered into the bone, often without a predrilled hole. This method of insertion caused friction and made it very difficult for surgeons to adjust the fixation of the wire. These limitations were overcome by the introduction of an electric drill in orthopaedic surgery, although this came with challenges of its own.
Today, K-wires are drilled into the bone, usually with minimal trauma to the soft tissue and tendons. This technique also enables surgeons to change the direction and position of the wire while it rotates.
The major drawback of drilling is temperature elevation, which has been known to cause thermal damage to the bone, leading to complications for the patient associated with the loss of osteocytes. Fortunately, manufacturers of K-wires have been able to mitigate these issues through clever design decisions.
K-wire designs
According to a recent research article, the design of the K-wire tip has a significant impact on debris removal and heat generation during drilling. As developed by Kirschner, the earliest K-wire design featured a diamond-shaped tip with two opposing flat facets.
Another common design is the trocar trip, with three bevel planes ending in a point. This configuration is capable of cutting smaller holes for a better fixation. Designers have also experimented with cutting slots and notches into the trocar tip to improve debris evacuation, which in turn reduces the rise in bone temperature.
Other point designs of the K-wire have been tested out over the years. For example, a third point configuration known as the Medin K-wire was introduced as an attempt to further reduce the thrust force, torque, and bone temperature rise associated with other tips.
Many more types of tips have been developed to accommodate specific indications and surgical techniques. It is clear that, despite the seemingly simple role of the K-wire, these pins are complex devices, where a well-designed tip can make a huge difference to the safety and efficacy of the treatment.
And when a K-wire manufacturer needs a custom-made solution for their next K-wire innovation, many companies turn to Custom Wire Technologies (CWT), a trusted US-based manufacturer of medical wire solutions.
Leveraging its extensive experiencing in wire grinding and top-quality equipment, CWT can manufacturer a range of K-wire tip designs for both ends of the pin (including trocar, diamond, radius, blunt, and conical) using certified materials such as 304V Stainless Steel, 316LVM Stainless Steel, or Nitinol (Nickel Titanium).
Find out more by downloading the whitepaper below.