
Ground-breaking new products and emerging markets are driving record growth in the global healthcare industry. Better technology is improving billions of lives and creating new opportunities for medical device manufacturers. In order to keep up with demand, an increasing number of companies depend on extremely high annual production rates.
Injection moulded plastic parts are quickly replacing traditional materials in medical devices not only because of their wide ranging material advantages such as sterility and design flexibility, but also because of the cost and speed at which they can be manufactured.
When productivity is measured in units of tens or even hundreds of millions, conventional moulding methods make way for specialised systems. Parts produced at such high volumes can be found in products ranging from disposable, one-use devices like syringes and diagnostic equipment to implants, clinical packaging solutions and other precision instruments.
High-cavity applications generally operate in round-the-clock, automated, clean room environments, running with fast cycle times and small shot weights.
Processing medical parts is particularly challenging because there is absolutely no room for error. To ensure patient safety, 100% of all parts shipped must adhere to the stringent quality standards put in place by industry regulators.
Injection moulders that need to achieve and maintain this level of quality at an output of several hundred million plastic parts a year from a single, high-cavity mould turn to high performance hot runner systems.
How well do you really know your competitors?
Access the most comprehensive Company Profiles on the market, powered by GlobalData. Save hours of research. Gain competitive edge.
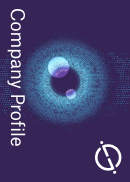
Thank you!
Your download email will arrive shortly
Not ready to buy yet? Download a free sample
We are confident about the unique quality of our Company Profiles. However, we want you to make the most beneficial decision for your business, so we offer a free sample that you can download by submitting the below form
By GlobalDataImproved efficiency
- Material gains
Hot runner systems are ideal for the production of medical parts because they offer consistently high rates of efficiency and productivity. Most notably, they cut production costs dramatically by eliminating unwanted scrap in the form of cold runners, including related part handling and loss of valuable material.
A cold runner is the by-product of moulding with melt distribution channels that cool, solidify and get ejected with each shot, or moulding cycle. In some cases, especially with very small parts, the material consumed by the cold runner can be far greater than that of the actual part.
Since many medical applications employ custom-engineered polymers, the excess material represents a major cost factor. Exotic thermoplastics can cost thousands of euros per kilo. In some instances, the extra material can be mechanically re-ground using auxiliary equipment and then reprocessed.
However, most medical applications permit only the use of virgin material for quality assurance and liability reasons.
The elimination of cold runners makes hot runners the preferred solution for clean room production. Simply put, the moulding cell remains ‘clean’ because the mould produces only parts and no waste, dust or other particle contamination.
Material suppliers offer a large variety of custom-tailored, medical grade plastics, engineered to have highly specialised, application-specific properties (e.g. bioabsorbables, lubricants and clarifiers). Most of these materials are difficult to work with because they are sensitive and can only be moulded within a small processing window.
If they are susceptible to heat or shear, special consideration has to be given to the design of the melt path, or the distance the material spends travelling to the mould cavity and how long it takes. Accurately controlling the flow of plastic using heat zones, shut off valves and cooling lines is a hot runner’s primary function.
- Faster cycle times
In the injection moulding world, cycle time is money. It stands to reason that one of the most effective ways to improve productivity is to make parts faster. This is easier said than done.
There are two basic ways to speed up production. The first is to increase the number of cavities, either in a single mould or through additional moulding cells. Adding more injection moulding machines to the factory floor is an easy solution, but a costly one. Operating new capital equipment, along with the energy and resources it consumes, represents a significant investment that will affect the bottom line.
The other option is to run the injection moulding machine faster. This may not be a possibility as there are physical limitations to how fast a part can be made. The material needs enough time to cool before the part is ejected from the mould, though optimised cooling in the mould can help lower cycle time.
Depending on the size of the part, the time it takes to fill the cavity is finite. For example, parts with a greater wall thickness are slower to fill.
Even the split seconds required for parts to drop out of the mould, or for robots to remove them, impacts on the overall cycle time. All injection moulding plants should try to push the capacity of their output to the machine’s limit.
Having an optimised part mould and hot runner design is the only way to achieve better, more competitive results. The hot runner is the engine that drives a faster mould.
It must be reliable under extreme heat and pressure, over millions of cycles. Designing and building these tools requires collaboration between expert teams with experience processing high volume medical applications.
Take for example, a large project with an annual production of 400m parts, such as disposable syringe plungers, each with a shot weight of 0.7g and an output rate of 90%. Using a single 350t (clamp force) injection moulding machine, this would require a 128-cavity mould running a cycle time of eight seconds.
This type of performance can be achieved by using a valve gate hot runner system. In high-cavity settings, valve gates help reduce cycle times significantly.
Consistent quality
- Precision control
One important measure of part quality is a clean gate, which is the point at which the material enters the moulded surface. Valve gating further improves a hot runner’s ability to deliver consistent quality and efficiency. Each individual gate can be opened and closed for precision control of the injection sequence, ensuring absolute consistency from cavity to cavity, and from shot to shot.
Valve gates offer more processing control than traditional thermal gates using hot tip nozzles because small changes in the processing parameters and fluctuations of the melt viscosity do not affect their performance. A larger processing window is of extreme importance in an automated 128-cavity mould running small parts.
When moulding micro parts (weighing less than 1g), a specific challenge is to maintain uniform melt distribution from the machine barrel through the melt channels (manifold) and the hot runner gates. In the example of the syringe plunger, a total of only 89.6g of material is distributed through the melt channel with each cycle to the 128 individual mould cavities.
To make this possible, the valve pins have to open and close at exactly the right time to control the flow. In order to produce consistent parts, the packing pressure and shear rate have to be balanced. The melt must maintain a uniform temperature in each cavity.
Accurate control of these parameters and the reduction of cycle times are the key functions of the valve gate hot runner. Sequential valve gate controllers or sequence controllers provide accurate control of the injection process by opening and closing multiple gates for optimised fill of the cavities.
Temperature controllers regulate the various heat zones throughout the system, maintaining the proper flow and integrity of the material. High end hot runner suppliers offer manufacturing solutions that allow the controllers and the sensors inside the mould to talk to each other in order to enable real-time data logging and production reporting for multiple injection moulding systems.
Sophisticated controllers and browser-based visualisation tools can generate a live online overview of multiple moulds and injection moulding machines, whether they are operating in a single plant or in various locations around the world.
Certain integrated analytics systems allow decision-makers to monitor, compare and analyse the performance of all the active moulding cells in a programme, anywhere, any time, directly from a smartphone or computer. All key parameters are securely logged, backed up on a special server and accessed through a remote, browser-based login.
Production output, downtime, failure reporting, machine status, operator performance – everything is available in real time.
- Go with the flow
Since most polymers can only spend a limited amount of time exposed to high processing temperatures, it is crucial that a detailed flow analysis is conducted before machining any melt channels. Especially in high-cavity moulds for small parts, where these melt channels branch off multiple times, an accurate rheological calculation is necessary to ensure an ideal melt residence time. In order to maintain their integrity, most polymers should not spend more than a few minutes travelling the length of the melt path from the machine barrel to the cavity.
Flow simulation software is used to model a balanced system that optimises melt residence time, pressure drop and shear rates inside the manifold and nozzle channels. The runner geometry, combined with the model of the mould cavities, creates accurate results that simulate realistic processing conditions. The final design is derived from and validated by this analysis. The importance of this step cannot be overstated since it eliminates uncertainty in the early stages of a project.
In the example of the syringe plunger, the total shot weight amounts to 89.6g (128 x 0.7g) and the runner channels contain 800g of melt. At a cycle time of eight seconds, it takes approximately nine shots to clear the entire melt path, resulting in a melt residence time of only 72 secs. This means that this runner layout will accept very temperature-sensitive polymers and additives without risk of degradation.
For the advanced production of quality plastic parts, such as the syringe plunger, a reliable hot runner design is made possible only through comprehensive analysis, quality components and an in-depth understanding of processing challenges.
There is no such thing as an off-the-shelf solution. When it comes to healthcare, there is no room for guesswork or error, but with a systematic approach, there is great potential for new, life-changing designs. Every high performance hot runner system must address both the fundamental and the advanced aspects of turning a great idea into reality.