
Medical applications of nitinol have soared in recent years, mainly due to its ‘memory’ properties and for its ability to take much more strain versus stainless steel. For surgeons needing to navigate in particularly tight areas, nitinol is both kink resistant and has the flexibility to change shape as needed.
Nitinol belongs to a family of alloys consisting of nickel and titanium. Extremely corrosion resistant, it also demonstrates excellent biocompatibility. Nitinol exhibits superelasticity with the ability to remember and return to a specified shape after deformation when exposed to a predetermined temperature. With transformation temperatures for superelastic grades between -20°C (-4°F) and 22°C [71.6°F), these ‘room temperature’ grades are more common in medical devices.
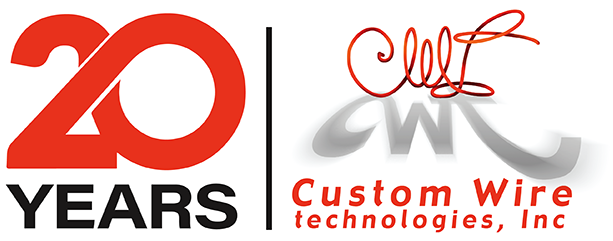
Over the last decade, Custom Wire Technologies (CWT) has seen nitinol’s use in the medical device industry boom. CWT is a medical wire solutions manufacturer with over 20 years of industry experience providing customers with custom manufactured medical components using a range of certified materials, including nitinol and stainless steel.
In 2010, CWT first used nitinol in a customised suture threader, in which the alloy’s shape memory properties ensured return to its original shape after passing through the small hole in the instrument, allowing medical professionals to load the suture more easily through the device.
Shape setting with nitinol
“Nitinol use at CWT has increased tremendously since 2010,” says Jim Boldig, director of sales and engineering at CWT. “We have open orders with our raw material supplier for quantities more than 18 million feet of a single diameter. One of our product lines is using roughly 200,000 feet per week. We have come to embrace the material. It works extremely well for core wire grinding and reinforcement coils for catheters.”
In terms of production, shape set nitinol catheter reinforcement coils are in the greatest demand, with CWT setting hundreds of coils per day and thousands of coils per week.
Additional applications include suture threaders. “We have several suture threader product lines that require a unique shape on the end of a shaft. The shapes are created with custom tools manufactured internally,” points out Boldig.
Working with nitinol can be challenging due to the material’s flexibility and abrasive nature, but over the years, the CWT team has built up a vast amount of expertise when it comes to shape setting.
“The biggest challenge is the shape setting process itself,” explains Boldig. “It requires additional space requirements from work-in-process (WIP) storage and equipment. Shape setting also requires heat treatment to achieve the correct specifications. This adds time to the process, so CWT is always investigating ways to manage space and time to be as efficient as possible and has recently invested in vertical storage for WIP and purchased new equipment that effectively is two machines in one.”
Looking ahead, Boldig says that he doesn’t believe nitinol, for all its advantages, will ever completely replace stainless steel: “There are many devices on the market that will keep stainless steel relevant. This could be driven by several things; costs, manufacturing methods, or regulatory approvals. Not all manufacturers have experience working with nitinol. New devices might make it to the market with nitinol but there will always be a need to support stainless steel. CWT will continue to support all necessary alloys for all customers.”
The future of nitinol
CWT has a longstanding relationship with one of the premier global suppliers of nitinol, which allows it to offer the latest cutting-edge advancements to larger OEM customers while also supporting start-ups. However, like most industries, the pandemic put global supply chain issues foremost on the company’s mind, and Boldig explains that CWT has taken steps to ensure their supply chain is robust, and customers are never disappointed.
“Prior to the pandemic we would source material when needed. Usually only enough material to satisfy job requirements. However, with the increase in lead times from suppliers we are purchasing to stock as well. In some instances, we are issuing orders for material 6 to 12 months out to help keep the supply of materials steady. We have orders on the books with releases into 2024 already.”
With the future in mind, Boldig looks forward to the next 10 years: “Demand and development in the transseptal access space will increase. Currently, several development programs are using stainless steel, and this could be an area where nitinol is adapted and used more frequently.
“However, it is the customer’s engineers who ultimately choose which material makes it into the device. CWT will embrace the demand to adapt to new manufacturing methods, such as wire EDM (electrical discharge machining), and laser processing. The technology of both methods fits into CWT’s vertical integration plans.”
To learn more, download the whitepaper below.