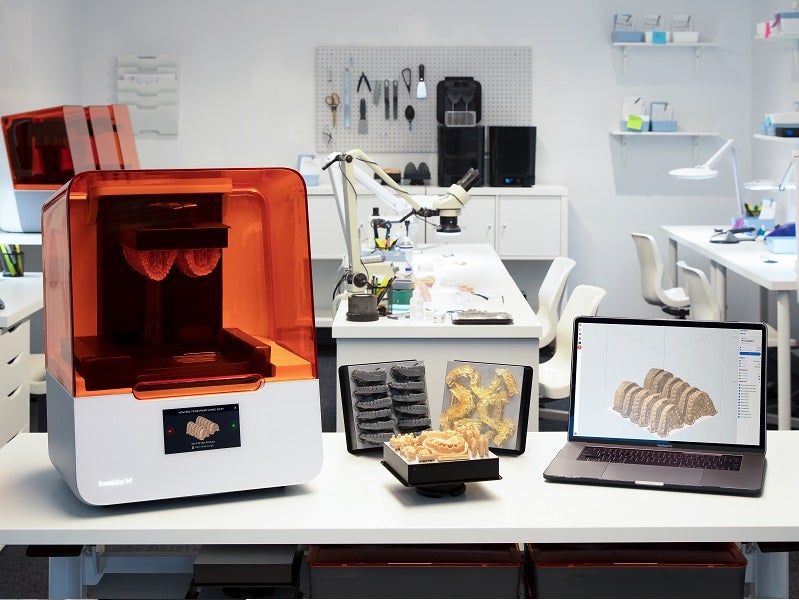
Dental implants are unusual in the field of medicine, in that everything installed in a patient’s mouth must be custom-made for that person. While other fields are just beginning to dip their toes into patient-specific solutions, dental implants have had to operate that way for years. There’s no one-size-fits-all when it comes to dentures or braces, and patients often need multiple iterations of the same mouthpiece as they work their way through different treatments.
This makes 3D printing an ideal fit for the dental industry, as it’s possible to make unique surgical guides, crowns and trays quickly and cheaply. There’s no need to go through the lengthy process of taking physical impressions and creating a plaster mock-up of a patient’s teeth to manufacture a device around. Instead, a 3D digital impression can be taken with an intra-oral scanner, a camera that can create a 3D rendering of the teeth and gums in a digital file. With all the right technology on hand, the device can be printed right then and there without the patient even having to leave their chair.
Digital Smile Design (DSD) uses this kind of process to plan and create dental treatments for patients, while 3D printing industry leader Formlabs has recently launched a new dental business unit. Chloe Kent asked DSD director George Cabanas and Formlabs dental project manager Sam Wainwright how 3D printing is being used in dental clinics today, and what it could mean for the future of dentistry.
Chloe Kent: George, how do you use 3D printing at DSD?
George Cabanas: The DSD Planning Centre has been a pioneer in using 3D printed technology for the benefit of dentistry, by assisting dentists in the planning of their patient’s treatments. DSD started years ago, with the creation of 3D printed digital models that represent the desired future state of the patient’s teeth after complete dental treatment.
These 3D printed models allow the patient to ‘test drive’ their future ideal teeth: the simulated end-result teeth are 3D printed and worn in the mouth to see and feel the difference. This helps reduce subjectivity in the communication between the patient and her dentist and ensures that the dentist, her team and the patient all share a common objective outcome to the treatment.
Today, the DSD Planning Centre can reduce the time that a clinician and her patient have to wait for their mock-ups, diverse guides and appliances to be ready. A clinician that has a 3D printer in her office can manufacture the DSD-designed product within minutes of approving the case.
CK: How is 3D printing going to change the dental industry?
GC: 3D printers are now affordable and within reach of all clinicians. This allows the clinician to have the DSD team assist them, and minutes after approving the treatment plan the clinician can 3D print the product in their office. The great advantage of this is that the clinician can access specialists from around the world but still manufacture the specific appliance for their patient locally.
Additionally, the clinician will be able to use 3D printed appliances to ensure the implementation of the treatment plan is followed closely. In the end, 3D printers in the office are a sign that the clinician is willing to invest in their practice and their patients by using the best tools possible.
Sam Wainwright: 3D printing and advanced photopolymers are the end-game manufacturing solution for the dental industry, and we are still in the very early days of this digital evolution. Better, more efficient treatments are found through the complete digital workflow in dental technology, and 3D printing is a huge part of that process.
When Formlabs entered the dental market in 2016, other competitor 3D printers in the space had been too expensive for most labs and private practices to bring the technology in-house. The Formlabs Form 2 printer drastically changed the dental market by providing highly accurate, easy-to-use 3D printing that every dental business can afford. With Formlabs and the new Form 3B, dentists have industry-specific support from a team of dental experts, access to the latest materials and applications through an extensive dental materials library, and validated print settings thoroughly tested by dental experts, making 3D printing possible for every dental business.
CK: Does the technology have any caveats?
GC: Today, high-quality liquid resins are used for 3D printing dental appliances. As these resins require local health approval, certain resins may not be available in all areas. This may complicate the access to better resins in certain parts of the world.
As good as these resins are today, the aesthetic result of a ceramic tooth is not yet capable of being printed. The variety of colour plus the translucency of ceramics is not yet achieved in resin. As a result, definitive fixed dentures will continue to be ceramics for the next few years. However, today we are starting to see conventional acrylic removable dentures being substituted by 3D printed ones.
SW: For a 3D printer to be fully utilised in the dental environment it must be part of a complete digital workflow that involves other pieces of hardware and software. This is very exciting because 3D printing allows digital dental workflows to become reality, but it also only allows the most cutting-edge dental businesses to adopt 3D printing technology.
CK: What are the most exciting developments happening in the field right now?
GC: There are two major fronts to the development in the 3D printing arena: new materials and speed of manufacturing. New biocompatible materials soon will start to mimic the aesthetic result of ceramics and innovation in transparent flexible resins that will have many dental applications. The rapid manufacturing speed will allow the dentist to manufacture the appliance for the patient while the patient is still in the dental chair.
SW: We are excited to see how fast digital technology and workflows are being adopted in the dental industry right now. Restorations, removable prosthetics and orthodontic appliances made with a fully digital workflow are better for patients, dentists, orthodontists and dental technicians alike. Formlabs Dental is committed to creating great 3D printers accessible to every dental business, no matter the size.