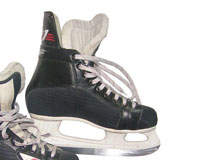
One of the areas that has historically been most challenging for device manufacturers, as well as one of the most expensive to get right, is injection moulding.
While the technology and the science within this area are complex, the reality for most device manufacturers is that it is not one that has undergone radical change over the years, argues John Beaumont, professor at the plastics engineering technology programme at Penn State Erie, The Behrend College, and founder of Beaumont Technologies.
“Though there have been subtle evolutionary advancements in injection moulding in recent years, there has been little done to eliminate the product variations that occur within a given mould and during a given moulding cycle,” he points out.
“The key challenge for engineers around the world remains the constant struggle with variation. Everyone is under financial pressure to reduce product cost. This generally leads to the use of hot-runner, high-cavitation moulds, but this is not an area that has been changing that much; there are few revolutionary changes or activities going on.”
Nevertheless, one trend that is affecting how manufacturers work and the pressures they are under is the drift towards miniaturisation, something that is creating challenges around geometrics and tolerances. Microfluidic devices, for example, will incorporate tiny, micron-sized channels that have to be manufactured with absolute precision if the flow of blood through the device is to be maintained at a consistent rate.
“Dimensions and tolerances are continually getting smaller and tighter,” says Beaumont. “The smaller the parts, the tighter the tolerances. It used to be that 25-50µm on a plastic part was a pretty tight tolerance, but more and more we are developing – and expected to produce – parts with features that can be 25-50µm with submicron tolerances.” There is also a trend towards bigger moulds, which in turn requires bigger machines.
“Within medical devices there is an increasing drive to reduce costs, so device manufacturers want to get as many cavities into a mould as possible,” Beaumont explains. “The larger moulds present a number of challenges, including the fact they must be structurally robust; the bigger they get, the more potentially unsupported regions there are which can physically deflect or move. This leads to the need for large machines that can handle the moulds but also maintain the high speeds needed to minimise cycle time.”
Melt-flow variations
Perhaps the biggest challenge facing device manufacturers is around variation in melt flow within geometrically-balanced – sometimes referred to as ‘naturally balanced’ – runner systems. Such flow imbalances have historically tended to be attributed to variations in mould temperature or mould deflection.
Most medical device manufacturers will lean towards hot runner systems because they are more economical but, as they are essentially heated tubes, they can create their own variation. It is well recognised, for example, that it is possible to get variation where the hot runner touches the cold steel of the mould, even with the use of air gaps to cushion and prevent such contact as far as possible.
But one possible source of variation much less widely recognised within the industry, Beaumont says, is “shear-induced melt variation”. This is a complex phenomenon: in essence, when plastic flows down a runner, the shear rate and temperature (and therefore the viscosity) will vary along and across the runner channel. The shear rate will normally be highest just inside the outermost regions of the flow channel and zero at the centre. The shear rate will also be high in the runner and gates of a mould, where the velocity of the melt is normally at its highest.
in injection moulding.”
A high shear rate near the outer wall can have a knock-on effect on viscosity and, in turn, on frictional heating, which can mean the melt in these outer laminates is above the temperature of the melt in the centre of the runner channel.
This can result in flow imbalances between cavities as these variations in melt conditions become divided into different runner branches, causing the material travelling down each branch to be at a different temperature, viscosity and flow rate.
“If you are injection-moulding plastics there is no turbulence,” Beaumont explains. “Rather, the plastic flows in a smooth stream referred to as laminar flow. As it moves along the stationary walls of the flow channel it creates frictional heating in the outer laminates of the stream.
“The difference between these outer and inner laminates is what creates the variations in injection moulding. These variations between outer and inner laminates can exceed temperatures of over 80°C and viscosity differences of 100-fold or more.”
This is a problem because, if a device manufacturer gets this sort of variation, it is all too easy to get uneven distribution of the melt and, in turn, uneven filling of the cavities. And uneven filling of cavities will result in the parts being formed differently.
One solution, particularly for those using geometrically balanced runner systems, is Beaumont’s own patented MeltFlipper technology. This rotates the melt, thereby repositioning the various melt regions to provide more balanced filling between the cavities. It’s an innovation which, he argues, results in a more balanced pressure, melt temperature and rheology between cavities, thereby minimising variations in the size, weight, shape and mechanical properties of the resultant moulded part.
“The improved control yields a wider process window with less variation and lower cost parts,” Beaumont adds.
Recognise the problem
Whatever the individual technological solutions reached by manufacturers, the key is first to recognise there is a potential problem that device manufacturers need to be addressing. The problem is often misunderstood and left undiagnosed as traditional means of inspecting parts, monitoring of the moulding process and even state-of-the-art injection moulding simulation programmes can completely miss the effect. This led Beaumont to develop the ‘5-Step Process’ to help moulders indentify shear-induced imbalances and separate them from the other common causes of product variation.
“Although I first published on this phenomenon back in 1997, much of the industry has been slow to realise the significant negative impact that it can have,” says Beaumont. “For a long time it has felt like it has been only a small handful of us preaching to the industry and trying to help. The variations and resultant problems you can get because of this are still not something widely recognised nor appreciated within the industry.
“It all stems from a basic understanding of polymer rheology and fluid flow in closed channels such as the runner of a mould. Both cold and hot runner moulds will result in significant temperature and viscosity variations between what is flowing through the runner’s centre and what is flowing along its perimeter. These variations will become dispersed into different cavities and even within individual cavities.
“There are means to control these variations, but they are limited. The first thing one needs to do is simply be aware of the problem. This is something the industry is still getting to grips with and which it does not fully appreciate the impact of. It is something that needs to be recognised and understood in order for the industry to evolve and fully optimise its potential in the moulding of medical devices.”