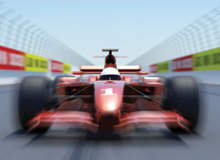
In product development, prototypes serve a valuable role as physical models that can be seen, touched and operated by designers to provide feedback during the development process. This is especially true for plastic medical devices, which are often designed to be manually manipulated by end users (doctors and/or patients) and which frequently must mate with other manufactured components.
The value of a prototype depends largely on three factors: the speed of manufacture (turnaround time), the accuracy in modelling the planned production part (dimensional, material, texture) and cost.
Historically, conceptual prototypes could be machined or carved out of solid blocks of clay, metal or plastic. While machining allows the planned production material to be used in the prototype, the quantity of parts that can be machined economically and quickly is low, and part geometry is limited to machinable features.
In some cases, parts are moulded in polymeric tools. For example, prototype parts can be produced using either room temperature vulcanisation silicone or polyurethane moulds.
These are inexpensive and fast to make, but have a limited tool life (25–50 parts) and offer only a limited choice of thermoset (rather than thermoplastic) materials.
In the past 20 years advances in technology have led to an assortment of methods by which plastic prototypes of complex geometry can be made in hours. These rapid prototyping techniques include stereolithography (SLA), fused deposition modelling, 3D printing and selective laser sintering (SLS), and are collectively known as additive processes (parts are built up from the addition of layers).
They generally provide very fast turnaround, adequate dimensional fidelity (although surface finish is often rough), and can be used for complex part geometries, but are limited in terms of material choice and part robustness, and are not practical for more than a few units. These methods can therefore rarely, if ever, be used for final part production.
Rapid injection moulding provides another alternative for medical device manufacturers’ prototyping needs, and is not a replacement for all previous methods of prototyping. Turnaround time, cost, part size and complexity, and material choice are all considerations when selecting the appropriate prototyping process. In general, rapid injection moulding bridges the gap between very low volume, fast turnaround, rapid prototyping methods and very high volume, slower turnaround conventional injection moulding, as shown in Figure 1.
Rapid injection moulding: what is it?
As the name suggests, rapid injection moulding uses the plastics production process of injection moulding, wherein plastic pellets are conveyed down a heated barrel and melted by a reciprocating screw, and are then injected at high pressure into a metal mould to achieve the final desired geometry. Virtually all thermoplastic polymers can be processed using injection moulding, and this remains the case for rapid injection moulding. In fact, the ‘rapid’ in the name refers not to a new kind of injection moulding, but an accelerated tool manufacturing process that can have a mould ready for production in days.
Advantages over other rapid prototyping methods include the use of the same material as will be used in the final part, and capability to achieve production quality surface finish. Additionally, the moulds produced can be robust enough for short production runs, allowing the same mould used for prototype production to be used for actual production.
Rapid injection moulding vendors have the capability to move from a computer-aided design (CAD) drawing of a part to a finished mould to prototype part production in days or weeks. This is in contrast to a lead time of weeks or months for a conventional injection mould.
There are several pathways to this shortened tool-making cycle used by various vendors. One path is to use CAD files to programme a computer numerical control (CNC) mill to machine the mould halves from aluminum, steel or hybrid materials (ProtoMold, Phoenix Proto Technologies, PTI Engineered Plastics).
Conventional injection moulds are produced from hardened tool steel by a combination of CNC machining, electrical discharge machining (EDM) and other methods, and often include a number of movable components in the mould such as side action lifters, sliders and core pulls that allow undercuts, throughholes and other complex features in the part.
Rapid injection mould production typically uses only CNC and includes limited (or no) movable components, placing some limits on the geometry of the part. There may also be limits on the total area of the part due to size limitations of the CNC mills used to machine the mould.
A second tool-making path is to use a CAD file to produce a SLA prototype part. The SLA part is then used to cast a mould from kirksite aluminum/zinc alloy or pre-hardened steel (Armstrong Mold Corporation, ICO Mold). A third path is to produce the metal mould directly from the CAD file by using SLS. This will yield a mould with a ‘powdery’ texture, but can achieve non-machinable features such as conformal cooling lines. A fourth path is to straddle the line between rapid and standard injection moulding.
Some vendors (such as Metro Plastics Technologies) will produce, on an accelerated schedule, a standard injection mould from tool steel, using CNC, EDM and mould inserts, sliders, lifters and core pulls for any part size and geometry. This requires a longer lead time than rapid injection moulding (weeks not days) and is typically more expensive than the CNC-only milling, SLA or SLS methods, but the absence of size or geometry limitations means the prototype is essentially the same as the production part.
Rapid injection moulding’s niche
Additive prototyping processes can provide one or more parts within a matter of hours. Conversely, conventional injection moulding can produce tens of thousands to hundreds of thousands of parts from a single mould that may take a month or more to fabricate.
Rapid injection moulding requires days to weeks, but allows a broader choice of materials, higher quantities, better surface finish, better material stability and tighter tolerances than can be achieved with additive processes (see Table 1). It can be used for short production runs of fewer than 10,000 parts, but is also faster and has lower initial costs than conventional injection moulding.
The cost per part of a process depends upon the number of parts to be prototyped or produced. For a handful of prototype parts, additive processes can produce parts inexpensively and quickly. However, the marginal cost of producing larger numbers of parts via rapid prototyping is high. On the other hand, conventional injection moulding requires a large initial investment of time and money for tooling, but can produce 100,000 or more parts at a very low marginal cost and time.
Rapid injection moulding fits between these two extremes, offering the ability to produce tens to thousands of parts at higher quality than additive methods, but at lower initial cost and faster turnaround time than conventional injection moulding, as shown in Figure 2.
Success in practice
Rapid injection moulding has been successfully used by a number of medical device manufacturers for a variety of applications (Table 2). While it is often used to shorten the design cycle for custom electronic housing assemblies, it has also been employed for specialised parts that play a key role in the function of the device, such as the polycarbonate cage of the Cytori Therapeutics Celution™ system, or the suture clamp for the American Medical Systems BioArc™ system. One provider, ProtoMold (Maple Plain, MN), has won recognition in the US for its rapid expansion, enjoying a 500% growth rate from 2003 to 2006.
Rapid injection moulding can offer an attractive option for production-quality prototypes and short production runs. The key enabling technologies for its development include the implementation of computerised methods such as 3D CAD software and the development of fast CNC machinery in an area that has historically been very labour intensive.
The turnaround time of days to weeks can allow multiple design iterations, ultimately leading to a better final product. Additionally, it can be used for ‘bridge’ production of parts while waiting for mass-production steel tooling. All of these advantages are attractive to medical device designers dealing with stringent performance requirements and increasingly aggressive timetables for product development.