
First used more than 2,000 years ago, paper has gone through numerous evolutions and applications, but the latest has managed to catch the eye of manufacturers the world over.
Yi Cui and his team working out of Stanford University in the US have developed a way of using paper – and now other materials – to provide energy for an array of devices.
Although not specifically designed for use within the medical arena, there is the possibility this new technique could offer an answer to the question of how to power portable or even wearable units in a way that has only ever been the stuff of science fiction.
As part of the research the team has incorporated nanotechnology into material, initially paper, as Cui explains: “We demonstrated high power and high specific energy storage devices by combining nanotechnology with well developed, traditional paper or textile technology.”
The paper is nothing more than that used in office printers around the world. “We demonstrated that we can coat cathode and anode materials directly onto paper with a simple dipping-drying process,” he continues. “We can also use paper or textile as a separator. Ultimately, we can fully integrate energy storage devices into the paper or textile.”
Power struggles
How well do you really know your competitors?
Access the most comprehensive Company Profiles on the market, powered by GlobalData. Save hours of research. Gain competitive edge.
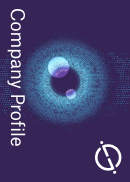
Thank you!
Your download email will arrive shortly
Not ready to buy yet? Download a free sample
We are confident about the unique quality of our Company Profiles. However, we want you to make the most beneficial decision for your business, so we offer a free sample that you can download by submitting the below form
By GlobalDataWearable devices are not new as previously reported in Medical Device Developments back in 2009. Then Dr Stephanie Lacour, engineering research fellow at Cambridge University, talked us through her RF antennas and components project. She hoped to develop devices that could be worn, like skin, and transmit real-time biological information for remote monitoring, drug administration and even mimic neural pathways between the brain and prosthetic limbs.
However, the biggest stumbling block was the power supply. “Whether electronic components are implanted in the body or grafted onto the skin,” she said, “they will require power and signal transmission to another remote electronic component such as a hand held device or laptop.
“With the antenna project, we want to explore if we can build such devices on soft materials, and how they would respond to mechanical deformation. In bioelectronics, you are really thinking about miniaturised elements and electronic components that interfere ‘mechanically’ very little, or not at all, with biological tissues.”
Perhaps this new innovation could be the answer to the problem. “One area where this form of power generation could prove to be beneficial within medical devices is health monitoring.” explains Cui. “For example, you can use our wearable battery to power up the integrated sensors. Solution process nanomaterial thin films have been widely studied for flexible electronics and displays, particularly on plastic substrate.
“Here we aimed at a totally new, emerging application with the change of substrate from plastic to paper or textiles. Supercapacitors and Li-ion batteries are devices with a sandwiched structure, which include anode, cathode and separator.”
Talking to the University’s own media network late in 2009 he remarked: “The process is very simple; it’s very low cost and very easy to do. We think this can really change the way people make batteries.
“You take a bit of paper, printer paper used for the copier machine, and put the nanotube ink, which is black in colour, onto it. You can either dip it in or apply it to the paper – paper itself has a highly porous structure. Once you have the paper with the ink applied you put it into an oven for a while and then you have a really conductive paper. It goes from being white coloured to black with the nantotubes applied.”
Inking a solution
However, the team has now moved on to applying it to fabrics. Writing in the journal Nano Letters in early 2010 they said: “Wearable electronics represent a developing new class of materials…which allow for many applications and designs previously impossible with traditional electronics technologies.”
Although it is now possible to apply electronic circuits to some fabrics thanks to a number of projects in recent years, the difficulty of applying them to the types of fabrics used in clothing has remained. However this latest work has provided a breakthrough. Having successfully demonstrated that nanotube ink can easily and cost effectively be used on paper the team found the interwoven nature of fabric was also a potential candidate.
By using the same sort of technique employed to apply the ink to the paper they were able to create batteries from fabric. They dipped the material into the ink and pressed it, thinning out the coating to ensure an even spread.
Speaking to the BBC, Cui said: “Our approach is easy and low cost while producing great performance. Fabrics and paper represent two technologies with a thousand-year-old history. We combined ‘high-tech’ – nanotechnology – with traditional ‘low-tech’ to produce new applications.” Surprisingly the fabric is able to keep its structure when folded, stretched, or even soaked in an acidic or basic solution.
There have been concerns about the use of nanomaterials in the past. Not really knowing how the particles will interact with the wider environment has been the issue of much debate in recent years. But Cui expresses his determination that the product is safe.
“People may hesitate to accept these devices due to the use of nanomaterials,” he says. “However, with good sealing of the devices using the well-developed technology from the semiconductor community, these concerns can be addressed.” He also thinks that regulation could be an issue but that this too can be resolved.
When looking at what the future could hold for this revolutionary product Cui says he is hoping to take advantage of the commercial interest he has already received.
“There are several companies that are interested in the commercialisation of this technology and so we believe it will be applied somewhere, sooner or later. With the continuing development and scaling up in production of carbon nanotubes we foresee the cost coming down further.”
The next step, he says, is to explore new device structures, integrating them into real devices and understanding their mechanisms. “We are focusing on the improvement of device performance and the understanding of device operation,” he concludes.