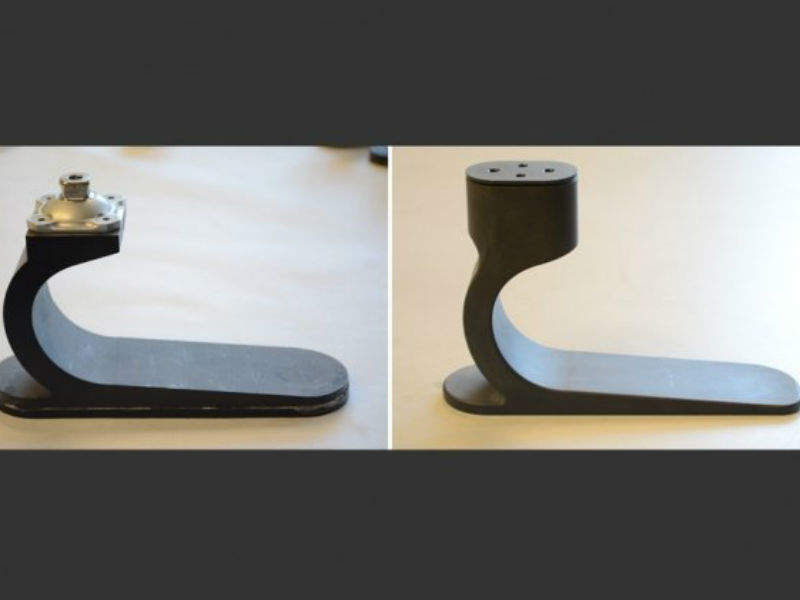
MIT engineers have developed a simple, low-cost, prosthetic foot that can be tailored for individual patients. By using a patient’s body weight and size, the researchers can tune the shape and stiffness of the prosthetic foot, allowing users to walk with an able-bodied gait.
The engineers estimate that if the foot is manufactured on a wide scale it could cost a lot less than existing products. Current high-tech prosthetic limb designs can cost tens of thousands of dollars, making them unattainable for many amputees.
MIT associate professor of mechanical engineering Amos Winter said: “A common passive foot in the US market will cost $1,000 to $10,000, made out of carbon fiber. Imagine you go to your prosthetist, they take a few measurements, they send them back to us, and we send back to you a custom-designed nylon foot for a few hundred bucks. This model is potentially game-changing for the industry, because we can fully quantify the foot and tune it for individuals, and use cheaper materials.”
The custom-designed prostheses are based on a design framework developed by the researchers that provides a quantitative way to predict a patient’s biomechanical performance based on the mechanical design of the prosthetic foot.
Winter and former graduate student Kathryn Olesnavage have reported details of this framework in IEEE’s Transactions on Neural Systems and Rehabilitation. They also published the results of their prosthetic foot research in the ASME Journal of Mechanical Design, with graduate student Victor Prost and research engineer William Brett Johnson.
The team wanted the mechanics of the foot to relate to how the lower leg moves while the foot is in contact with the ground. To do this, they used an existing dataset containing measurements of steps taken by an able-bodied walker with a given body size and weight. With each step, previous researchers had recorded the ground reaction forces and the changing centre of pressure experienced by a walker’s foot as it rocked from heel to toe, along with the position and trajectory of the lower leg.
Winter and his colleagues then developed a mathematical model of a simple prosthetic foot simulation, which described the stiffness, possible motion, and shape of the future prosthetic. They used the ground reaction forces from the dataset to create the model and predict how a user’s lower leg would translate through a single step.
With the model, they then tuned the stiffness and geometry of the simulated prosthetic foot to produce a lower-leg trajectory that was close to the able-bodied swing.
The team then sought to identify an ideal shape for a single-part prosthetic foot that would be simple and affordable to manufacture, while still producing the desired leg trajectory. The group ran a genetic algorithm to decipher the most optimal designs.
To test the prosthetic, the researchers produced several feet for volunteers in India.
Winter said: “What’s cool is, this behaves nothing like an able-bodied foot, there’s no ankle or metatarsal joint, it’s just one big structure, and all we care about is how the lower leg is moving through space. Most of the testing was done indoors, but one guy ran outside, he liked it so much. It puts a spring in your step.”
The team is now collaborating with Italian rubber outsoles manufacturing Vibram, which is working to design a life-like cover for the team’s prosthesis, which will also give the foot some traction over slippery surfaces. The MIT researchers plan to test the prosthetics and coverings on volunteers in India.