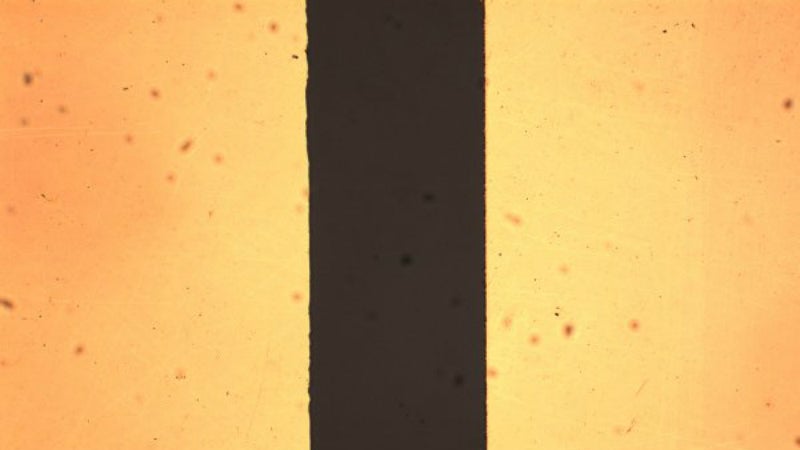
Laser Competence Centre Finland (LCC Finland) covers the whole development chain including technology oriented basic research, end users’ application development, system integration and testing of lasers as well as training aspects.
The objective is to adapt new laser technologies to the needs of industry so that the companies can experiment and develop their products and their processes by utilising the know-how and hardware of the centre.
Laser Pilot Factory (LPF), an application laboratory of LCC Finland, has been running for one full year at Tampere University of Technology (TUT). It has been proven to be a successful concept: new type of lasers were tested and evolved, new applications found and nurtured.
This service model has clearly met the demand from industry. The most important single factor here is the fruitful co-operation between industrial end-users and laser development partners in LCC Finland.
Ultra short pulse fibre laser hits record speeds
LPF has been in the front line of application development for an ultra short pulse fibre laser. LPF is running now the 3rd generation of Corelase X-lase ultra short pulse fibre lasers and the current version fits in many needs in modern manufacturing. The most promising applications are found in laser surface structuring and thin-film ablation.
Laser surface structuring
Precise surface structuring of steel or specialized hard coatings is a promising application for an ultra short pulse fibre laser. Precise grooves and shapes with minimal thermal effect offer a competing advantage for functional surfaces. Challenges lie in processing speed, process parameters and design of micro shapes.
Thin film grooving
High repetition rate and relatively high power allow very high processing speed for a thin film removal for an ultra short pulse fibre laser. Removal speed typical clearly exceeds 2m/s. This high speed is already a challenge for a workpiece manipulation. Typically laser power and removal speed can be adjusted so that it removes cleanly just the required layer.
Medical applications
By laser machining micro-grooves and holes to the implant/product it is possible to manufacture biodegradable filters and other applications e.g. to guide nerve tissue growth. In addition, it is possible to coat implants to protect the implant structures or use the coating as a drug carrier, change surface topography to enhance cell proliferation or improve corrosion resistance and wear resistance.
Scalpels, bone saws, microsurgical instruments and implants are typical examples of laser machined applications. Laser cutting has also been used for cutting stents and needles. For example in stent production, cutting stent implants to desired shapes becomes difficult due to the decreasing diameter of the desired tubes.
Very small cutting width, small heat affected zone and the damage free interior of tubes during laser machining are challenges in stent production. Typical stent materials are stainless steel, cobalt and chrome alloys, nitinol, tantalum, platinum and niobium, but nowadays biodegradable polymers have also been used.
Laser joining as a manufacturing method has been used for hermetically seal pacemakers, defibrillators and neural stimulation devices. Various biomaterials have been successfully joined together by means of laser joining e.g. polymer-polymer, glass-metal and polymer-metal. In the future many potential applications for laser joining will rise in the field of biomedical sector.