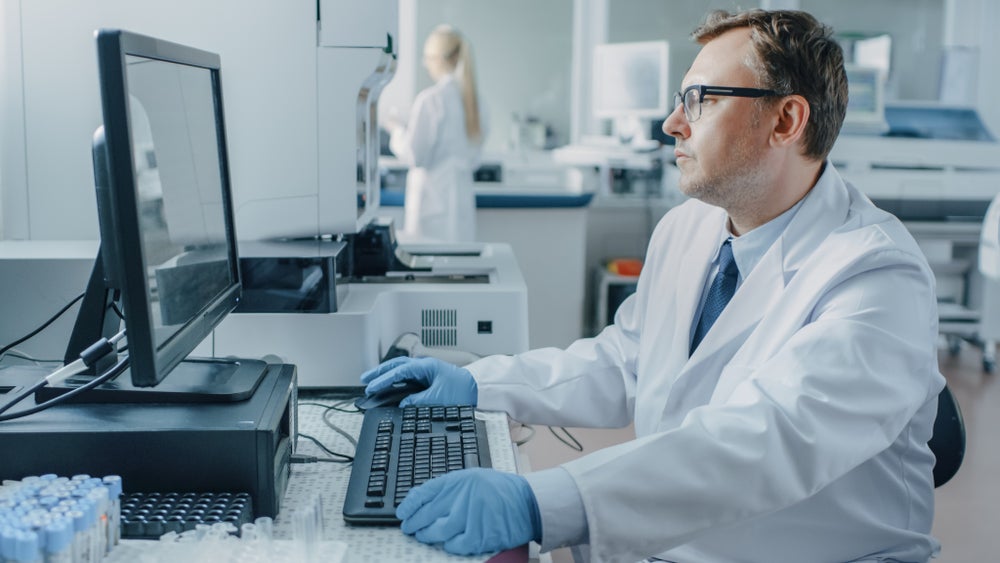
Hosted online, eIFU offer a tempting range of benefits for both the manufacturer and the end user. However, the shift doesn’t come without challenges. eIFU are heavily regulated, and their implementation involves major internal operational changes. That’s where IFUcare steps in, offering a single supplier solution to facilitate the process of implementing eIFU so that manufacturers can reap the long-term benefits.
Switching to eIFU
The advantages of switching from paper IFU to eIFU should not be underestimated. One of the most obvious benefits is that by cutting out the physical printing of IFU, manufacturers can save on paper and printing costs. In addition, removing the paper booklet from the medical device packaging means that a smaller box can be used, reducing the materials required for packaging and increasing the number of packages that can be stored in the warehouse. These resource-saving measures not only cut costs for manufacturers, but they also reduce their environmental impact.
In manufacturing itself, removing paper IFU can hugely simplify the process by eliminating the step of inserting the paper booklet into the box. This mitigates a source of potential error and removes the need for a checking stage to ensure the paper document is going into the box.
eIFU makes manufacturers’ lives easier in other ways too. If the content of the IFU needs to be modified or updated due to regulatory nonconformities, for example, it is far simpler to do so online than to replace paper IFU. eIFU can be updated regularly and instantly, without affecting material inventory, and involving far less labour than replacing paper IFU. This gives manufacturers much more flexibility and reduces the chance of IFU-related product recall.
On the customer side, eIFU offer a much-improved user experience. Paper IFU are typically characterised by small font, designed to fit information into as small a space as possible. Usually, the document includes many different translations of the same information, among which the user must select the one they need. In contrast, eIFU can be viewed on devices like tablets or computers, creating greater possibilities for design and layout. eIFU can even incorporate interactive or dynamic elements, such as click-through processes, animations, or voice prompts, and make it easy for the user to access the most helpful version of the information.
Furthermore, with eIFU customers don’t need to worry about losing a paper document or separating it from the product, because they can always be easily located. As it’s hosted digitally, eIFU are not subject to wear and tear in the way that a paper document is.
In the industry, some companies have concerns about the risks of eIFU compared to those of paper IFU, which have been around much longer. But in many ways eIFU is safer. Important information is more legible and accessible for the customer, and there are no restrictions on the amount of data that can be provided, thereby reducing the likelihood of user error.
How IFUcare can help
The switch to eIFU is a significant one, and the challenges involved should be acknowledged. It will affect multiple operational stages, including instruction design, labelling inventory management and packaging and logistical processes, as well as requiring web platform management. In addition, eIFU are subject to stringent regulatory, functional, and operational requirements which require significant effort on the part of the manufacturer.
However, over the long-term this investment creates value for companies by reducing workloads across the manufacturing process, cutting direct costs, and increasing operational efficiency. And outsourcing the implementation of eIFU means taking this burden away from manufacturers, allowing them to realise the benefits quicker.
This is where IFUcare steps in. As a pioneer and global leader in eIFU implementation services, the company facilitates seamless eIFU implementation. Developed by regulatory experts, IFUcare’s services focus on compliance and risk management, meeting all EU, FDA and national requirements and regulations for eIFU. It also facilitates full traceability by logging all user and administrator actions, while guaranteeing a multilingual website interface for optimum useability. This can all be tailor-made to suit the specific requirements of the manufacturing client.
Dirk Stynen, founder, and president of IFUcare, says: “We were the first in the market to offer this as a service. Our service is very much compliant, in addition to meeting the more obvious requirements, like being easy to use.”
For manufacturers who are ready to embrace the benefits of eIFU, IFUcare can reduce the burden and accelerate the payoff.