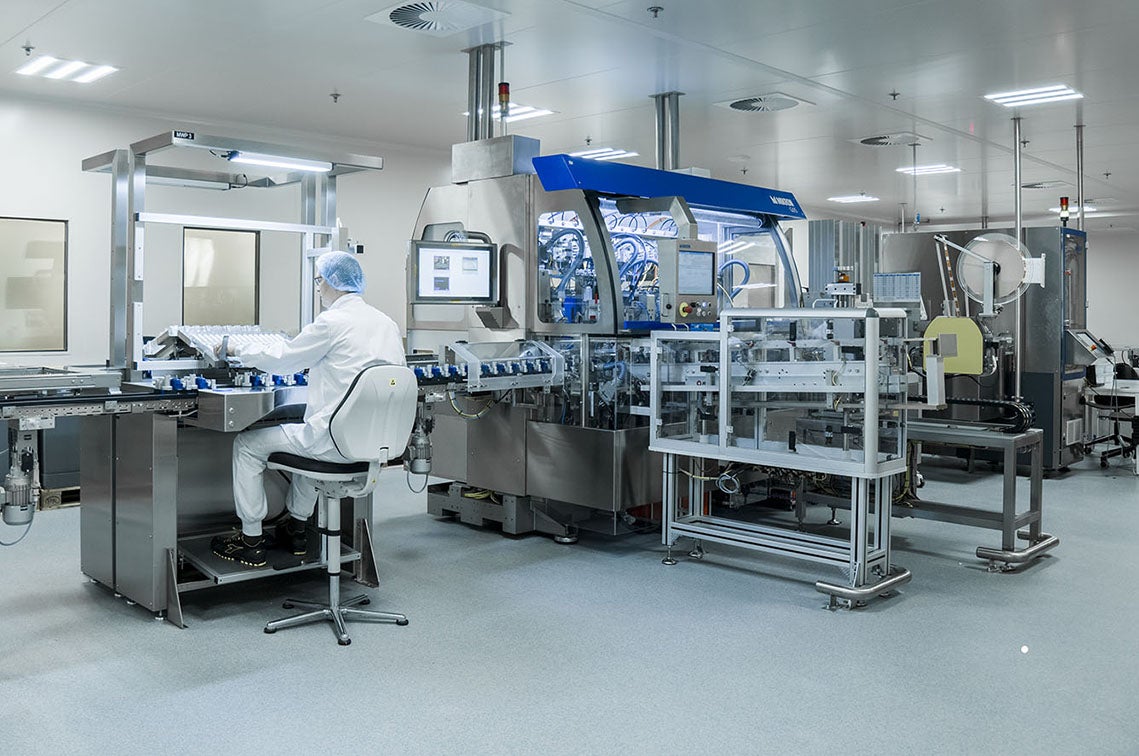
With more stringent regulatory standards, shorter product lifecycles and more competition than ever before, the medical device industry is evolving at an unprecedented rate. New technologies, markets and patient requirements are emerging, along with increasing demand for self-diagnostic and treatment devices. To keep abreast of such a dynamic, challenging market, manufacturers must take the right approach to building assembly systems.
“Manufacturers need to reduce their development time, fast-track validation processes and launch their devices according to the evolving needs of the market,” says Jean-François Bauer, head of marketing and business development at leading assembly solution partner Mikron Automation.
“Today’s market belongs to the assembly solution provider which can integrate flexibility and scalability. The rapidly evolving market demand requires Mikron to be nimbler than ever and accelerate our customers’ production capabilities, all while helping customers optimize their investment.”
Process equivalency: The power to scale up
The medical device market is projected to grow from USD 455bn in 2021 to USD 658bn in 2028, according to Fortune, fueled by an increasing number of surgical and diagnostic procedures. And manufacturers are investing more than ever in innovation, with Johnson&Johnson having invested around USD 12bn in R&D in 2020.
As the medical device market grows and diversifies, with the emergence of more new complex devices and players than ever, manufacturers face huge competition. It is increasingly important to slash time-to-market, and assembly solutions often have to be designed before all the details of a new device are even known. Assembly solutions must keep up with both increasing market volumes and progressive financial investment.
Since the 1970s, Mikron has been known for designing standardized assembly platforms based on ‘building blocks’, as well as mastering complex assembly processes. This unique set of capabilities forms the foundation of Mikron’s scalable automation solutions.
“A huge benefit of Mikron’s scalability concept is that we develop and validate processes in the early phase,” says Bauer. “This ‘process equivalency’ enables manufacturers to start small, achieving their first launch using a semi-automatic line in as little as four months.
“Thanks to our ‘building block’ concept, they can reuse processes that are already validated as they ramp up with more sophisticated and automated lines. This is very important in pharma, where once something is validated it is difficult to change.”
Mikron Automation sites offer scalable platforms based on specific market needs, enabling the gradual scale-up of automation and production volume. Giving manufacturers the ability to adjust their capacity in line with market demand significantly lowers their risk.
Speed and agility
Manufacturers are also increasingly recognising the importance of a flexible production line in order to remain competitive and react to the demands of the market.
“Today, manufacturers need more flexibility than ever,” Bauer explains. “In the last ten years, generic drugs have arrived on the market, opening new markets with new patient needs.
“The number of medical device variants has increased, and batch sizes have decreased. There is a new demand to run different products on the same line, meaning that manufacturers need to be able to adapt and retool the system quickly.”
As the production line scales up, flexibility can be built in. The challenge is integrating flexibility without losing productivity, Bauer adds: “Speed and flexibility are usually a contradiction,” he says.
Where more flexibility is needed, servo-driven technology, robotics, flexible conveying systems and smart control systems can be integrated into the line, enabling different product variants or devices to be run on the same production line . The flexibility of the line and tooling is complemented by Mikron’s flexible feeding system, Polyfeed.
“The key is finding the balance between several different types of technology to enable flexibility while maintaining productivity,” says Bauer.
The Mikron difference
Swiss-based Mikron Automation specialises in flexible, scalable and customised assembly solutions that evolve with the product lifecycle, from product development to maximum performance production.
Mikron has 50 years of expertise in developing complex processes, helping customers to mitigate their risk when the device enters the industrialization phase. To support customers in the early stages, Mikron offers not only assembly systems but also a full set of services, from DFX (design for assembly, design for manufacturing) to pFMEA (process failure mode and effects analysis), supported by PoP (proof of principle), clean room assembly trial and validation support. These services allow the customer to mitigate their risk both technically and financially.
For customers, Mikron is a one-stop-shop for developing and scaling their assembly solution as the product develops, cutting out the risk of involving different partners and giving manufacturers the agility they need to respond to the market.
Mikron is known for producing high-quality, high-performance assembly solutions, built for purpose in close partnership with its customers. As the medical device market continues to become more complex and competitive, scalability, flexibility, expertise and high-end services promise to become ever more crucial to manufacturing success.
To learn more about Mikron Automation solutions, download the whitepaper.