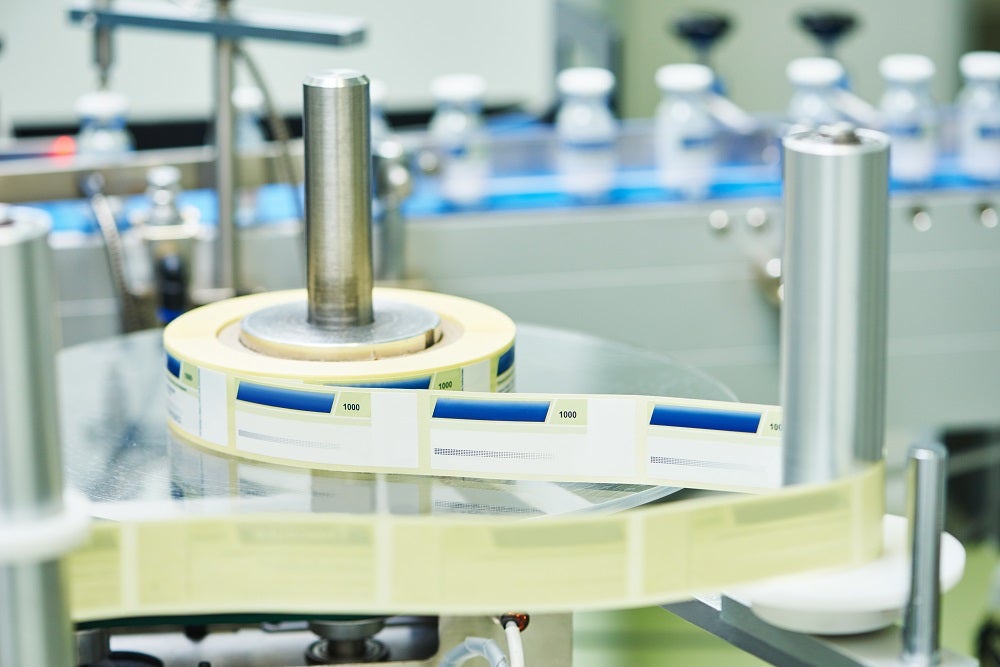
When it comes to pharmaceuticals and medical devices, safety is a top priority, but packaging and labelling is often overlooked. This is starting to change, however, as companies begin to realise that accurate labelling is actually a major safety concern, particularly with the introduction of new rules such as the Medical Device Regulation (MDR) and the In Vitro Diagnostic Regulation (IVDR).
More goes into medical device labelling than one might initially think. All too often, mismanagement can lead to companies having to delay rollout if they cannot comply with regulations, offer transparency, or ensure that all printed labels are accurate.
Medical Device Technology spoke with Beth Peckover, vice president of operations at global labelling solution provider Kallik about the importance of an effective label management system for medical device companies, and how its Veraciti solution makes migration to new software a breeze.
Up-to-date data
According to Peckover, the first step is helping customers to understand and access what data they already have: “When it comes to migrating data into our system, customers often have different databases that are stored in various locations.
“Typically the data is held in different systems because varying product lines and units of the business might have their own ways of handling data and labels. This means that trying to get that information is often quite difficult and can take longer than they anticipate. Often the focus is on signing the contract to start the project as soon as possible, when in fact the customer also needs to be gathering their data ready for the project start.”
As well as compiling their data, customers also need to consider the quality of their data and ensure that it is clean and up to date, so Kallik works with customers to cleanse that information of any inaccuracies or repetition.
“We’ve seen before that customers can have a dataset that is several versions out of date from what’s on the label, so there’s a risk that they would be importing out-of-date data into the system.
“Sometimes we will identify where there’s a need to rationalise content. They might have two phrases that are very similar and saying the same thing, and we only want one version of an image or an icon in our system because you want to control that latest version.”
More than a software provider
Many industries are going digital, so artificial intelligence (AI) and advanced technology is increasingly being used to migrate data and manage labelling systems.
“What we’re doing for one client at the moment is a proof of concept around using artificial intelligence to extract the data from the labels. This tool scans your label for the content and then processes it in a way that identifies where there’s commonalities to standardise and cleanse automatically.
“Once they can provide us with their labels, we make it easy for our clients and we effectively do the rest. Plus, with the AI tool that we’re using, we’re capable of loading labels and migrating into our system even quicker than we were before and to a higher level of quality because there’s less human intervention needed in that process.”
Migrating to a new management system can be a frustrating and complicated process, but Kallik’s Veraciti packaging and labelling management software helps to bring transparency and agility to the end-to-end labelling process. Ultimately, the migration to Veraciti is eased because Kallik is more than just a software provider; the company offers end-to-end professional services to implement the solution and migrate existing data.
“We have a team that is very experienced in getting our clients implemented and migrated, so they know the pitfalls and the things to watch out for and are able to advise clients. Each printer can be very different with its own quirks, so it’s really important that customers understand what those might be and how that might affect the label that is produced.
“We specialise in the medical device sector, so we’re very familiar with the requirements of medical device labelling and our team is there to make the customer’s journey as smooth as possible.”