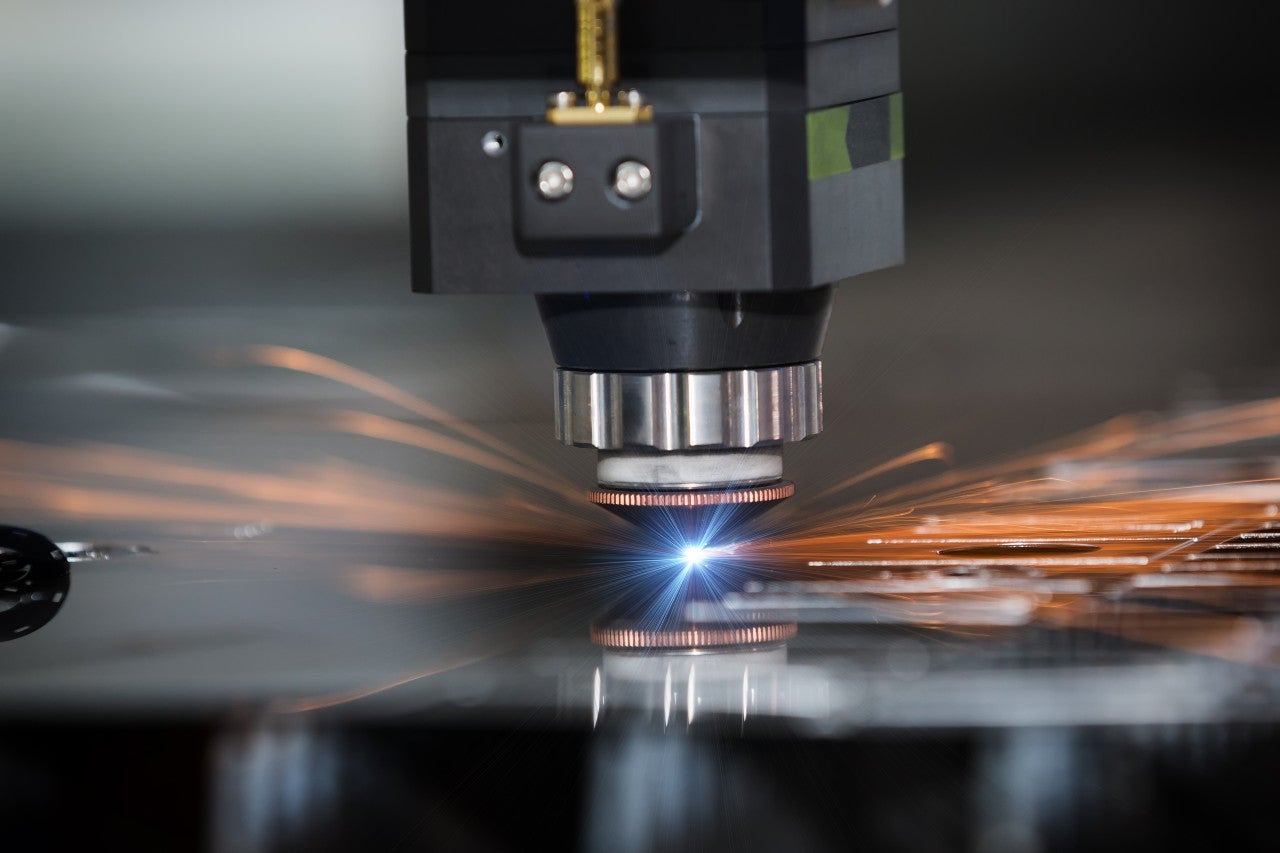
Medical devices are shrinking. It’s been two years since the Food and Drug Administration approved Abbots Laboratories’ 15mm transcatheter for premature babies, and five years since Medtronic’s Micra, touted as the world’s smallest and first leadless pacemaker, was marketed.
Miniaturisation is a trend that has a positive impact for everyone. Smaller devices enable doctors and patients to choose minimally invasive operations. Instead of performing life-threatening open-heart surgery, for example, doctors can use narrow catheters and guidewires to insert these tiny, life-saving devices via the blood vessels. As a result, minimally invasive surgeries with smaller medical devices are associated with less pain, reduced risks, and quicker recoveries.
With manufacturers designing ever-smaller devices, they require increasingly precise technologies. Laser beam welding is a popular example used across many industries. It is often associated with fine jewellery manufacturing, where precision is an absolute necessity. At the same time, it is increasingly being turned to as a way of joining materials in the medical technology field.
Why medtech manufacturers choose laser welding
Laser beam welding is an important technology used to join materials such as metals and plastics together. The process involves directing a laser beam at the target material. Because the beam is amplified and highly focused, its concentrated source of heat allows for narrow yet deep welds. This is known as a high depth-to-width ratio and translates to greater precision for medical device manufacturers.
The choice whether to use laser welding is highly dependent on the design application and the material composition, however. “There are instances where either a glue joint or a mechanical bond are superior depending on the composition of the materials being joined. Where the materials are similar, laser welding provides superior strength and ease of assembly,” explains John Corsten, head of sales at Custom Wire Technologies.
Based in Wisconsin, US, the engineers at Custom Wire Technologies (CWT) are specialists in fine medical wire. CWT’s core capabilities include coiling and grinding, but as the demand for this offering has grown, the company has also built a portfolio of value-added services that have transformed CWT into a one-stop shop for medical wire components. These include a range of finish processes that enable customers to complete their projects in the most efficient manner possible, and among them is laser welding.
Reducing lead times on complex device components
CWT uses YAG laser technology to weld ultra-fine wire components together, with a speciality in small-diameter medical wire. CWT’s most common welding projects include stents, hypotubes, guidewires, ball tips, sensors, cannulas, and needles, among additional wire devices.
“Laser welding is a value-added service that customers can take advantage of to have additional process assembly steps accomplished under one roof,” says Corsten. Finding a single source for producing individual components and joining them together leads to drastically shortened lead times for CWT customers, he adds.
CWT is working hard to tackle the big supply chain hassles for medical device manufacturers. Traditionally, complex medical devices with an array of components mean complex supply chains with an array of suppliers. By offering its laser welding capabilities and other value-added services, CWT is ensuring this doesn’t have to be the case.
To find out more, download the whitepaper below.