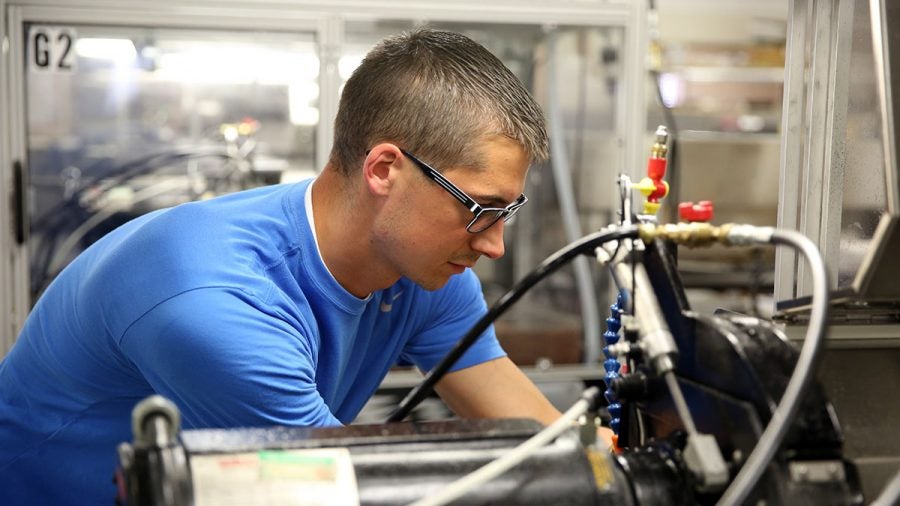
From tubes, shafts and clips to syringes and catheters, the medical device industry is home to a vast array of curved and complex surfaces which need to be marked. Not only this, but their markings must be consistent, repeatable and precise, and they are highly regulated.
Pad printing is a tried and tested method which has proven to enable high-throughput, compliant and economical marking, even on curved surfaces. It is a popular approach across industries for high-quality marking, and medical device manufacturing is no exception. Using the finest in computerised pad printing equipment, Custom Wire Technologies’ (CWT) pad printing service is one part of the company’s best-in-class OEM offering.
What is pad printing?
“Pad printing is the process of printing a two-dimensional image on a three-dimensional object,” explains CWT founder and president Bob Boldig. “The process is simple. A positive image, called the ‘artwork’, is etched into a photo polymer or thin metal plate. A sealed magnetic cup then rides along this plate and deposits a very thin layer of ink into the etched image and wipes everything else away cleanly.
“Then, a pad, generally made from silicone, presses down on the ink deposited in the artwork, picks up that image and then traverses and deposits the image onto the substrate that is being printed.”
The treatment process can be automated by using an integrated robotic feeding system, which precisely positions and rotates the product to be printed, boosting accuracy and reducing the chance of product rejections.
Flexible solution for a rigorous market
In the highly competitive and tightly regulated world of medical devices, pad printing offers a host of benefits to manufacturers. A principal benefit is its flexibility. “Pad printing can be used for an unlimited number of markings and identifiers, from corporate logos or user information to marking bands for device insertion depths,” says Boldig.
At the same time, the process enables printing on a range of surfaces, including uneven and three-dimensional surfaces. And switching between these capabilities can be done quickly and easily, meaning that syringes, catheters and tubing could all be printed in the same day without a great amount of operation downtime.
As well as this, pad printing has proven to work on a huge number of complicated and varied substrates, which are increasingly prominent in the industry. It does so without altering the product, unlike marking methods like heat pressing.
Compared to alternate methods of device marking, such as adhesive labels, pad printing tends to remain more permanent, Boldig points out. It is also often more cost-effective than other options, especially in the case of high-volume small parts. Another advantage of pad printing over the alternatives, Boldig adds, is the ability to use colour: inks for pad printing can be mixed to match any colour.
From a safety and regulatory perspective, pad printing ideally lends itself to medical device applications such as band marking, where the product will be inserted into the human body, because it can be used with Class VI grade medical inks, which are approved for use inside the body. As well as this, pad printing can allow for serialisation or issuing product number identifiers if required for FDA tracking compliance. In an industry which is characterised by stringent regulation, it is imperative to use a marking solution which facilitates compliance.
The CWT approach
CWT’s pad printing services fall into its range of competitive, precise and timely services. CWT typically prints on catheters, tubing, K-Wires and a variety of stainless steel and nitinol components for the medical device industry. By combining pad printing services with its cleanroom and ISO 13485 process, CWT achieves the outstanding levels of quality and precision which are essential in this market.