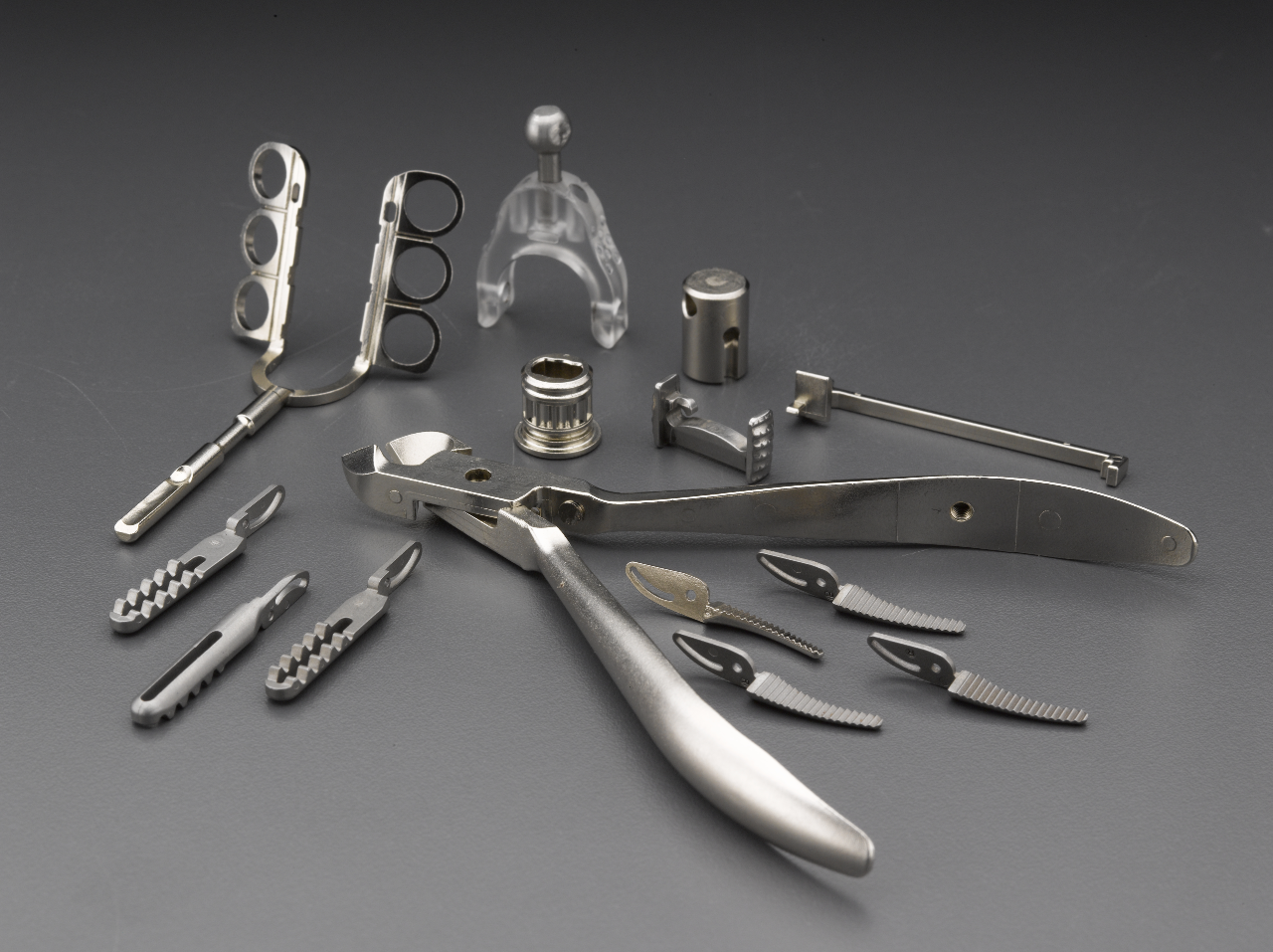
With ‘Industry 4.0’ just around the corner, manufacturing is no longer simply converting raw materials into an end product. Manufacturers are constantly innovating and optimising their processes, with new trends emerging and paving the way to the future of manufacturing. Krishna Chivukula Jr, CEO of INDO-MIM, gives his insight into how metal injection molding (MIM) fits into that picture.
Unlocking value across industries
Identifying and unlocking extra value is an advantage for any manufacturer, and MIM presents multiple opportunities to do just that.
“The first thing to understand about MIM is that it’s a very scalable high-volume component-forming technology,” says Chivukula. This means that manufacturing processes, once developed, can easily be scaled up to handle medium and higher-volume production. MIM can also provide features that traditionally would require secondary operations, such as machining. By eliminating the need for these secondary operations, manufacturers can save time and money.
There is further value to be unlocked in the design stage if products are optimised for MIM production. “This could involve understanding what the really critical tolerances are and what can be relaxed, for example, or it could mean taking two parts of a process and joining them, thereby reducing the number of steps required,” explains Chivukula.
These opportunities apply across industries. In particular, the medical device industry, the automotive industry, the North American firearm industry and the manufacture of mobile phone components in China, are all key areas which will continue to benefit from the use of MIM.
“The really big new market that always seems like it’s on the horizon, but hasn’t quite emerged yet, is the aerospace industry,” adds Chivukula. Aerospace OEMs have generally been slow to accommodate technology shifts due to the critical nature of engine or sub-system components. But Chivukula says he’s observed these OEMs beginning to adopt MIM, and that it’s a trend that looks set to continue.
Development and evolution
In any industry, keeping pace with future trends requires timely and strategic adaptation. This is no different for MIM providers.
On the one hand, the development of products for MIM is likely to continue to improve. “Knowledge and awareness of how to design for MIM will continue to grow, especially in the automotive, firearms and medical industries,” says Chivukula.
This will go hand in hand with the development of new materials for use in MIM. For Chivukula, it’s important to be proactive when it comes to developing new materials. “If you’re out there actively developing materials, and then looking for applications after the materials have been developed, then you should start finding them,” he says. “This is especially true if you have a sales and marketing team looking globally.”
Titanium and complex alloys are increasingly popular materials across sectors. “We’re seeing more and more requirements for these advanced materials starting to emerge from customers,” adds Chivukula.
As well as this, manufacturers should be prepared to embrace new technology and processes to complement the role of MIM. “One of the key things that we’ll see is the development of additive processes,” says Chivukula, adding that this may involve incorporating selective laser melting and metal printing, for example, and sometimes substituting them for molding. “You may displace over the next few years worldwide some of the molding processes for additive processes,” he says. Additive processes such as these should provide advantages including increased design complexity, shorter development times and quicker speed to market.
“Certain players in the MIM industry who grab hold of this technology will be better positioned to service manufacturing requirements globally as the scope for additive applications expands,” Chivukula predicts.
Embracing the future
Growth prospects for the industry are good, and INDO-MIM is prepared to remain at the leading edge of developments. “Our role in terms of MIM is going to be as a global supplier with global operations,” Chivukula explains.
The company’s first overseas operation in San Antonio, Texas, servicing the North American firearm and medical device industries, is doing well, and INDO-MIM is looking to expand into Vietnam to service Asia, and primarily China.
INDO-MIM’s expertise in terms of materials is helps the company keep up with future trends. Chivukula highlights the importance of the company’s knowledge of “powders, particle size distributions, and how particle morphology affects the printing process”. Developing materials allows the company to offer customers better properties and enhanced chemistry control, as well as the ability to tweak properties to optimise cost and performance for their own applications, Chivukula says.
The company is also responding to growing customer demand for supply chain consolidation. “We’re moving into sub-assemblies and moving up the value chain in terms of the services we offer around MIM,” says Chivukula. “That’s something we’re doing on a global basis, and something we’ll continue to expand upon over the next three to five years.”