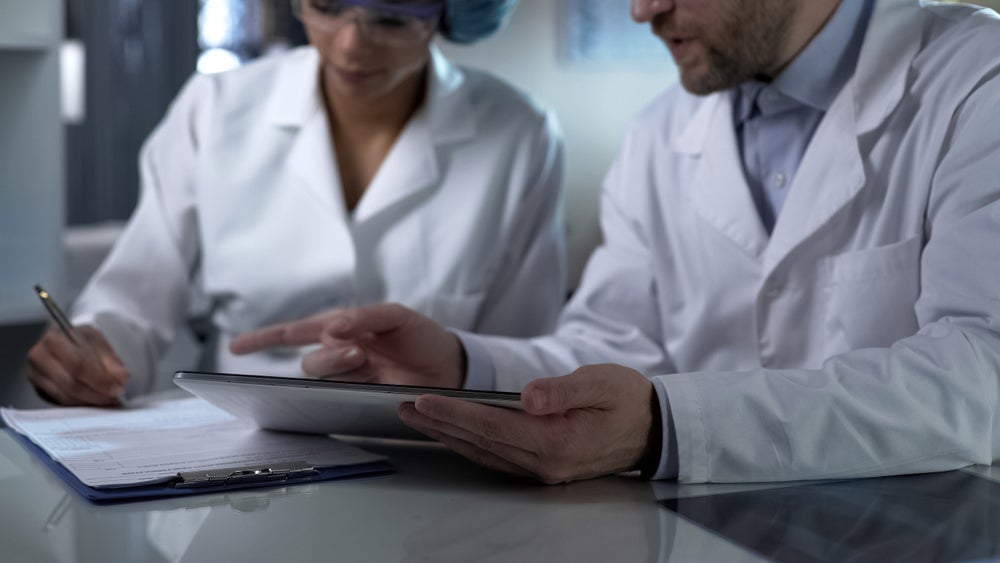
Since switching to eIFU affects a huge number of important processes and constitutes a significant change in quality management system (QMS), notified bodies (NBs) go through a rigorous validation process. Manufacturers should be aware of all the regulations and guidelines they need to abide by.
There are a whole host of benefits to be unlocked by transitioning to eIFU. Outsourcing the switch to a trusted provider can take away the regulatory burden from the manufacturer and pave the way to smoother, future-ready operations and a better customer experience.
Before you begin
The first thing for manufacturers to consider is whether eIFU is accepted for their type of products. According to European Commission regulations, eIFU are currently allowed for certain categories of medical device (MD), including implantable MDs and in vitro diagnostics (IVDs) for professional lab use. Outside the EU, the types of devices for which eIFU is allowed may vary from country to country, so manufacturers should pay attention to relevant national regulations.
In the EU, Regulation 207/2012 provides the requirements for MDs, and MEDDEV 2.14/3 (2017) contains guidelines for IVDs. NBs will verify that the eIFU’s functional specifications clearly address these requirements.
As well as this, standard 7.3 of EN ISO13485:2016 applies to the design and development of medical devices, and EN 62304:2016 applies to their design and life cycle management. Since many manufacturers consider IFU as part of their device, eIFU platforms should meet the same requirements. This may not be essential but helps to establish solid control and mitigate any possible compliance issues.
The NB will verify that the new eIFU, including the online platform itself, meets all the necessary requirements. One of the most important factors is that customers must be able to obtain paper IFU on request.
Making the switch
When it comes to making the switch, manufacturers must inform the NB of their intention and prepare for an audit. The change to eIFU must be done in line with the company’s change control procedure, and this includes performing an in-depth risk analysis, which will be verified by the NB. Having a system to provide a paper copy of IFU to users is one necessary risk mitigation.
The company must update IFU procedures, and create new procedures where necessary, to account for the switch to eIFU. Steps must be taken to ensure IFU and eIFU remain identical, in line with industry regulations. For example, printing and handling requirements for paper IFU are reduced, but employees should have instructions for how to validate, upload and update eIFU on the online platform. The procedural changes include informing customers in advance that the switch is being made and letting them know where they will be able to find eIFU. Regulations specify that this information must be on the device or packaging, the most effective method being to print a URL on the label. NBs will examine this procedure.
The labelling itself must also be updated. For one, the label should display an easy-to-understand symbol which indicates that eIFU is available. It is also important to make it clear how customers could request a paper copy of IFU, for example by providing a phone number. All of this will be checked by the NB.
Having changed to a digital format, manufacturers also now can make their IFU more user-friendly by enlarging the font, using colour, including high-resolution images and video. This is where the benefits of eIFU come into play – making IFU easier to understand and improving customer experience. Splitting files into different languages can also make IFU more accessible.
A helping hand
Manufacturers can significantly reduce their workload and increase their compliance by choosing to outsource the switch to a qualified, reliable supplier. The supplier must be notified as a critical supplier, and the choice of supplier must be justifiable to the NB. Suppliers with ISO 13485 and ISO 27001 will be easier to justify.
IFUcare’s service has been developed by regulatory experts over more than ten years, with a focus on compliance and risk management. Manufacturers using IFUcare’s eIFU solution can be confident that the platform, supplier, and validation process meet national regulatory requirements – reducing their burden and allowing them to enjoy the benefits of eIFU.