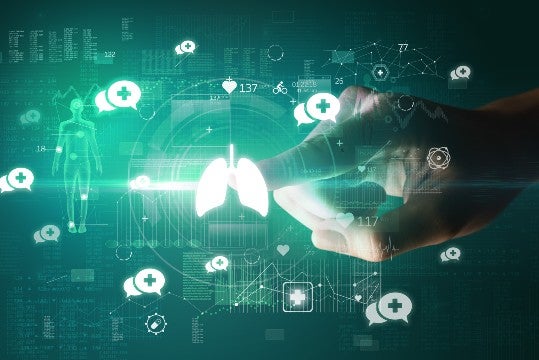
Developing and manufacturing a medical device is no easy process, and the challenges are arguably compounding as costs and quality requirements increase. Medical Device Network explores the top five challenges facing medical device original equipment manufacturers (OEMs) in 2022.
1. Quality concerns and product recalls
Poor quality in a medical device is a serious issue, as it could lead to end-user injuries or worse. This is especially important for high-risk medical devices such as pacemakers, coronary stents, and artificial heart valves. Such products must go through a particularly rigorous regulatory review process to ensure they are safe and reliable for patient use.
If a problem with quality is observed after a batch has been shipped, a product recall should immediately be issued. Such an event can devastate a brand’s reputation as well as the company’s bottom line. In fact, quality-related issues are thought to cost the medical device industry between $2.5bn and $5bn a year.
2. Counterfeiting
Counterfeit medical devices are on the rise, posing a serious threat to patient safety. In 2010, the World Health Organization reported that 8% of all medical devices in circulation are known to be fake. While more recent figures are hard to come by, the current number is expected to be much higher.
Many publications have reported an increased rate of medical device counterfeiting, fraud, and trafficking since the Covid-19 pandemic. The most widely affected product markets tend to be thermometers, PPE, orthodontics, test kits, and contact lenses. Fortunately, anti-counterfeiting technologies are helping the industry fight back against these fake, mislabelled, or tampered-with devices.
3. Regulatory compliance
The risks to patient safety associated with medical devices has led this industry to be one of the most tightly regulated. Depending on where a medical device company intends to market its product, there may be multiple different standards their product must comply with.
The journey to receiving regulatory clearance can be long and arduous, after which manufacturers must ensure they maintain production standards and continue to conduct post-market surveillance across the product’s lifetime.
4. Cybersecurity
Medical facilities are becoming increasingly vulnerable to cyberattacks, where bad players compromise IT systems with ransomware. We saw this happen to the UK’s National Health Service in 2017, when the WannaCry attack caused disruption across the nationwide hospital network.
Traditionally lacking the security found on other network devices, medical equipment can be an easy way for hackers to gain access to a whole server. In the event of a compromised device and a server takeover, hospitals risk equipment outages and patient data breaches.
For this reason, medical device manufacturers have an important responsibility to ensure newly made digital devices are equipped with the appropriate cybersecurity software going forward.
5. Disrupted supply chains
As highlighted during the Covid-19 pandemic, the global medical device industry is vulnerable to supply chain disruptions and stock shortages like most other industries. But unlike others, the sector can struggle to find quick solutions, whether that be a new supplier or a small change to a manufacturing line.
Once a medical device has received clearance, its production must follow the processes outlined in the regulatory submission exactly, with any change to production requiring re-qualification and validation. A disruption or delay in the supply chain can therefore set medical device OEMs back a long way.
The Covid-19 pandemic is not the first nor will it be the last time that supply chain disruption affects the medical device market. Companies should be prepared and vigilant by starting procurement as early as possible and continually evaluating and mitigating any vulnerabilities in their supply chain.
As a well-established supplier of custom-designed medical wire components including reinforcement and Nitinol coils, core wires, wire forms and orthopaedic pins, Custom Wire Technologies (CWT) was a reliable, much-valued partner to medical device OEMs during Covid-19. CWT worked throughout the pandemic, fulfilling orders and even introducing an expedited delivery programme, QwikCoil, which aims to provide custom-made coils within a week.
Dedicated to delivering high-quality wire based components and assemblies that satisfy all applicable customer requirements, CWT is the medical device industry’s one-stop-shop saving companies around the world both time and money. As OEMs navigate their way through the challenges of the industry and its supply chain, they can trust in CWT’s ability to deliver the safety-critical components needed for their innovative medical devices.