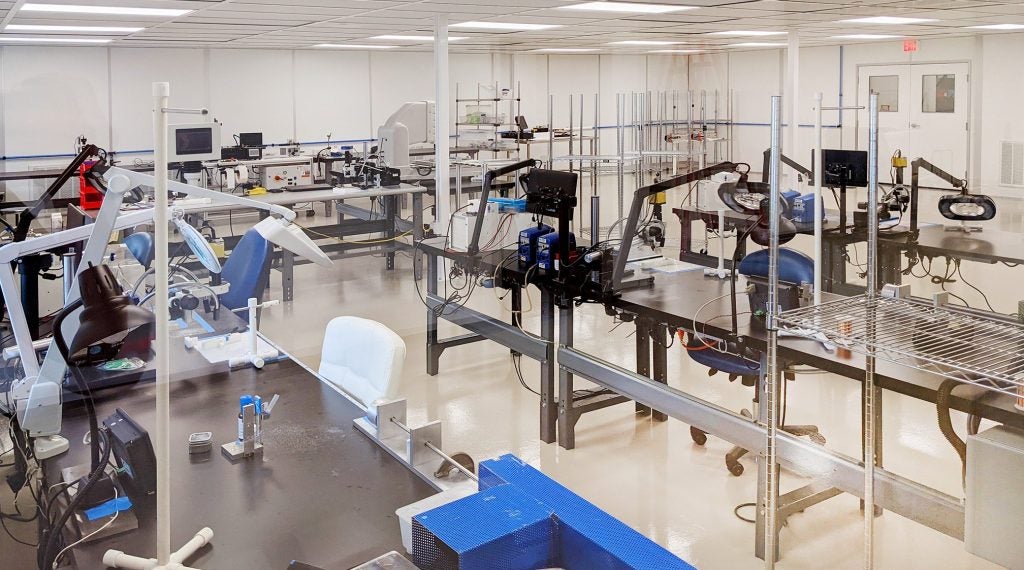
Strict quality and hygiene standards go without saying when it comes to medical device products designed to be inserted or implanted within a patient’s body. While often invisible to the human eye, particulate debris and bioburden are everywhere. If they find their way onto the surface of a medical device, that device becomes contaminated and, in worst case scenarios, could end up doing the patient more harm than good.
Used widely in the medical device manufacturing industry, cleanrooms are highly controlled environments with a focus on air cleanliness and particle concentration levels. In a cleanroom, effective air filtration is essential to reducing the level of airborne particulates. High-efficiency particulate absorbing (HEPA) filters are used to remove at least 99.97% of dust, pollen, mold, bacteria, and any airborne particles with a size of 0.3 microns (µm).
All cleanrooms are classified according to the cleanliness level of the air inside them – from ISO 1 to ISO 9. ISO 1 cleanrooms have the strictest standards, with air required to contain less than 2 particles larger than 0.3µm per cubic meter. A very small number of ISO 1 cleanrooms are used around the world, as this level of cleanliness is only required in highly specialised tasks typically in the field of nanotechnology. Most cleanrooms in the pharmaceutical and medical industries are ISO Class 7 or ISO Class 8.
With over 20 years of experience coiling, grinding, and forming medical wire, Custom Wire Technologies (CWT) supplies custom surgical components to medical device OEMs. The US company’s recently expanded facility houses a 2,000ft2 cleanroom designated for device assemblies, sub-assemblies, and product packaging, as well as a range of value-added services such as soldering, plasma welding, hydrophilic coating, inspections, pad printing, and ultrasonic washing to suit custom needs.
“By controlling contamination like bioburden and particulate debris, we can protect the integrity of the processes and manufactured product,” says Brittany Vanderhoof, technical process engineer at CWT. “CWT has an ISO-certified Class 7 cleanroom. Our cleanroom can have a maximum particle concentration of 352,000 particles per cubic meter.”
Validating and maintaining CWT’s ISO 7 cleanroom
As soon as a new cleanroom has been constructed, it must undergo a series of qualifications to ensure it meets the appropriate ISO standards. The validation process for Custom Wire Technologies’ cleanroom started with an installation qualification, which ensured that the structure is sound, the surfaces are level and secure, and the power and air filtration are functioning.
The next step in validation was an operational qualification, which assures no flaws exist that would prohibit certification of the structure, or any equipment necessary for manufacturing. Lastly, the performance qualification required the cleanroom to meet the standards of ISO 14644 for initial certification.
After validation follows the implementation of rigorous procedures to ensure standards continue to be met. “We have implemented controls to maintain adequate levels of cleanliness. Most importantly, our employees are trained and adhere to proper gowning methods to reduce fibres, skin cells, hair, and other debris that could introduce excess bioburden and particulate from the individual.
“Other controls involve a strict cleaning schedule that is executed in such a way to reduce contamination, a monthly monitoring process for particulate concentrations, and routine maintenance on our HEPAs to ensure they are working and changed at appropriate intervals,” explains Brittany Vanderhoof.
To maintain ISO Class 7 certification, the CWT cleanroom is recertified on a biannual basis. This is where a certified supplier visits the facility to assess the particulate levels, air exchanges and leak testing of the HEPA filters, verify positive pressure, and complete bioburden testing of the air and on horizontal surfaces to certify cleanliness.
In the past year, numerous improvements have been made to CWT’s cleanroom. Upgrading from soft walls to hard has fully enclosed the room, making its environmental conditions easier to maintain.
To accommodate for growing demand for CWT’s services, the company added 50% extra manufacturing space to its cleanroom, enabling the team to continue engineering and assembling an increasing number of high-quality components for the medical device industry.