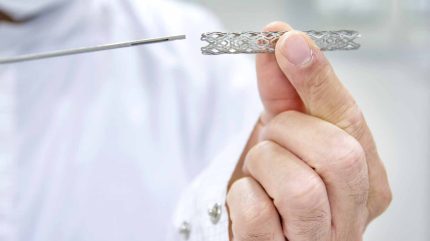
There is much talk of vertical integration within medical device companies, but this is often out of reach for small and medium sized businesses without the resources of a major manufacturer.
However, there are options available to streamline processes and make them more cost-effective – from concept to the finished product. For example, obtaining an optimal coating to introduce a medical device to the market typically involves dealing with several different vendors and partners, which can result in inconsistencies and delays throughout the product development cycle. Without the right coating, a medical device will almost certainly struggle to compete in the current market, leaving the manufacturer unable to generate revenue.
This is where Formacoat, a Medical Device Coating Application House in the Minneapolis, MN area, can be an accessible option for a company in need of a coating solution. Formacoat can provide vital solutions across a number of areas within medical device coating applications. While the US-based company does not produce the coatings, it stocks almost 100 different types of coatings from over 45 suppliers – and has the capability to refine solutions when an off-the-shelf solution doesn’t meet all performance or market requirements. Furthermore, the family-owned company also offers initial screening services for coatings from one facility.
“We can test the device on four or five, six different vendors’ coatings and eliminate or tune them as necessary in an initial coating screening, which is helpful for streamlining the initial development,” says Brecon Gross, manager of manufacturing engineering at Formacoat. “It also reduces costs because you’re not paying startup costs to multiple firms to get your project in the door, and then our timeline is one timeline versus balancing multiple timelines.”
Consultancy services for medical device development
What sets Formacoat apart further is its host of innovative R&D capabilities in-house, with a team willing to experiment to find the optimum solution. The company also has 3D printing machines to enable testing of coatings for devices with complex geometries, even from drawings in the early stages of a concept before a full device has been assembled. For newer companies or smaller businesses, these services can provide significant savings in time and money.
According to Brecon Gross, many of the development companies they’ve worked with do not have in-house expertise in chemistry, which can result in flaws or complications in design concepts for devices that are intended to operate inside the body. Many folks attempting to vertically integrate find developing and applying coating a challenge due to the depth of knowledge and understanding required when selecting a coating.
“With a lot of our smaller customers who are on the more innovative side, the concept may work. But we say: ‘Here are some factors we think you should reconsider’. There are not many chemists and chemical engineers at a lot of these companies,” he says.
“So, when you’re taking into consideration the interactions or even the biology and the biochemistry of things, there are missing pieces in people’s concepts. That is something that we try to work through with our customers.
“While at the same time, if they have specifics of their development or limitations in their current design, it’s helpful to leverage our experience while trying to work with and around them.”
While full vertical integration for medical devices may not be possible for many manufacturers, in the coating world Formacoat is able to fulfill many of the requirements – from the early stages of development to the application of the coating in a production environment. Brecon Gross prefers to think of this as part of a horizontal integration process.
“We’re talking about rapid prototyping or turnarounds – that is what we offer,” he adds. “We can handle your coating development or product development with fast fabrication. It’s not vertical in the sense of a supply chain, but it is in our world – expanding across the network of coatings that are available. So, horizontal is the new vertical.”