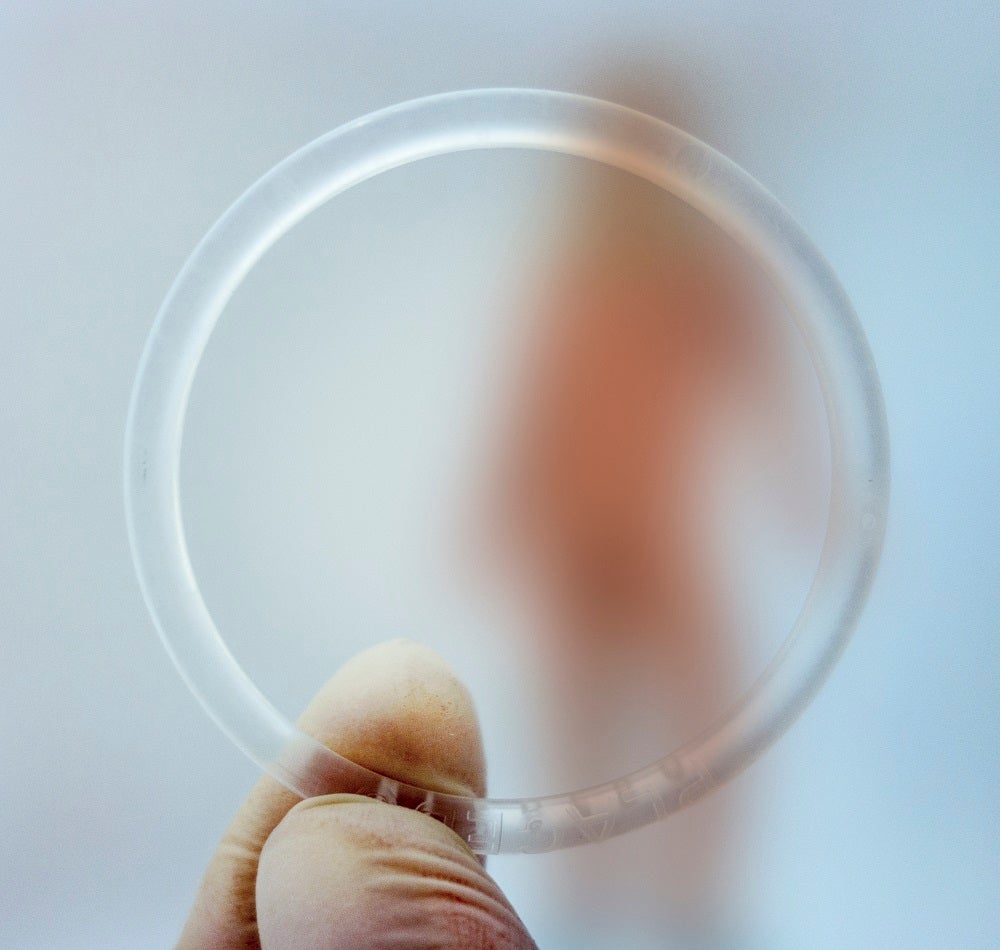
Medical-grade silicones are an efficient excipient for active pharmaceutical ingredients (APIs), suitable for long-lasting, long-term drug eluting solutions. Unlike bio-absorbable devices that typically only last months, silicones are especially suitable for patients with long-term conditions, eliminating any patient compliance issues.
Silicone has been the ‘gold standard’ for many implantable devices for more than 60 years due to its ability to cure into a permeable matrix structure. This creates space for API to inhabit and gradually pass through to the delivery point.
Methods for silicone to interact with API
When it comes to biocompatible silicones, the industry has a number of options available. An important consideration before a manufacturer selects materials based on the features that they require, is which method will be used to treat the silicone for it to interact with the API.
Whether you choose a full blending approach prior to cure, curing the silicone to act as a reservoir, or use a solvent-API solution to impregnate a cured component – each method has its own impact on the integrity of the silicone and present different challenges for the development process.
With this in mind, how can manufacturers choose the best silicone material for their implantable drug delivery devices?
High Consistency Rubber/Heat Cured Rubber (HCR)
Suitable for continuous, simple designs, HCR has a clay-like consistency in its raw state, giving it a stronger green strength that enables the holding of a shape while heat is being applied to cure the material. Typically, advantages include higher tensile strength, elongation, and tear strength.
HCRs attain a higher density when they cure, which can be used as a mechanism to control elution rates. With HCRs, manufacturers can use the extrusion process in order to make tubes or profiles. This continuous process also allows for automated cutting that can produce large quantities of simple parts quickly.
Liquid Silicone Rubbers (LSRs)
Offering the widest range of designs and suitable for mixing with API, LSRs are designed for moulding applications, most commonly injection moulding. For implantable drug delivery devices, LSRs can be full standalone devices or combined with other substrates via over-moulding.
The main advantage LSRs offer is the capability for the widest range of component design potential due to the ability to flow into much smaller geometries than HCRs and the fact that injection moulding can be fully automated. Additionally, mixing API into LSRs is simpler, without the necessity for creating a masterbatch.
Adhesives
Adhesives work in conjunction with other components and are designed as a complement, not a standalone item. With flexibility and accuracy of deposition, and many cure options, they perform multiple roles, including bonding elements together and being able to elute an API.
Adhesives can be deposited extremely accurately using manual or automated dispensers, making them ideal for a cure-in-place drug delivery element, as well as ensuring that the correct amount of silicone eluting an API is placed where it is needed.
Modifications
Manufacturers may consider silicone modifications for implantable drug delivery devices, such as dispersing HCRs and LSRs with solvents to create thin silicone membranes. This method, combined with an API, creates a drug-eluting conformal coating on a device.
Manufacturers can also use specially formulated foamed silicone or foaming agents to create more porous components for larger molecule APIs. Additionally, silicone foams are soft, which may provide more patient comfort.
However, both these modifications require longer development and lead times – compared to standard HCR or LSRs – to get precise control of layer thickness and to establish a consistent foaming process.
Selecting the correct silicone solutions
Sean McPherson, senior business development manager at Elkem, has spent over 20 years working within the medical device industry. His extensive experience means he can advise customers which silicones are best suited for a variety of projects and applications, all with different requirements.
“It’s a collaborative approach,” McPherson says, “the first thing to understand is from a physical standpoint, what does the drug eluting device look like? What is its goal? Is it to hold a structure as well as a drug or is it purely to elute the drug?”
McPherson explains that by fully understanding the aims of the finished device, Elkem can better understand the design:
“For example, a pessary device has to have a certain structure because it has a support feature, but then if [the customer] wants to add a drug solution element to it, what does that need to do? These physical and design type considerations are very important.”
When it comes to elution, McPherson says that understanding what the goals are will change what type of material a customer requires. This is especially important for elution rates that can span several years.
“If you need to achieve a very high elution rate, you probably want to go with something like an LSR that’s fully blended with an API in order to make sure you maximise the exposed surface area. That will give you a higher elution rate,” McPherson says. “[However] if you put a regulating sheath over it, using an HCR, over a drug blended core, that will help to control the elution rate. This may be critical in order to achieve elution rates that last multiple years.”
Silicones are a tried and tested technology, adds McPherson.
“It’s the gold standard for biocompatibility because of the 60 plus years of in-the-field, actual, real-world testing,” he says.
Working closely with customers across various industries worldwide, Elkem Silicones provides innovative silicone solutions, and offers a full range of HCRs, LSRs, and adhesives to meet the strict requirements for implantable drug delivery devices.
For more information, download the paper below.