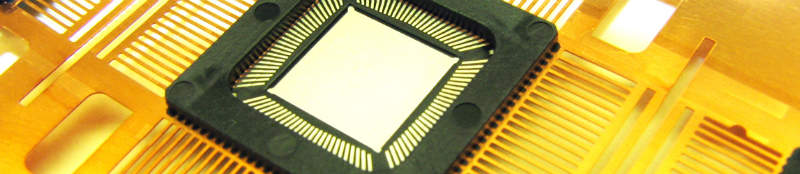
Not every mould is straightforward. Accumold’s capabilities are constantly expanding and improving because its customers never stop developing new technology.
In the same way that the company’s customers push it daily, Accumold pushes their understanding of what plastic can do, even with extremely small-part geometry.
Accumold’s speciality micro moulding continues to define what possible will mean tomorrow.
Microstructure enhancements
Accumold combines small and micro-sized parts with the ability to mould microstructures on the surface of the part.
These features can measure under one micron in size and are used in a wide variety of applications such as diffractive optics, micro-fluidics or microlenses.
Two-shot micro moulding
In micro moulding, two different plastic materials are shot in sync during a single operation.
Accomold’s customers use this type of micro moulding process to lessen the amount of labor required, create a more robust part configuration, or increase cost savings.
This process also is capable of handling other applications, such as cosmetics or touch-and-feel applications.
Insert speciality micro moulding
Insert micro moulding encapsulates in a wide variety of materials such as metal, glass, fabrics, flex-circuits and other delicate media.
Similar to those created with two-shot moulding, these parts not only reduce handling and assembly they can solve critical issues in manufacturing.
LDS / 3D-MID
A complementary process to specialty micro molding is laser direct structuring (LDS) or often referred to as three-dimensional moulded interconnected device (3D-MID).
This selective plating process is a perfect fit for Accumold’s Micro Mold® technology. Inquire about partnering with Accumold for your micro molding part of this process.