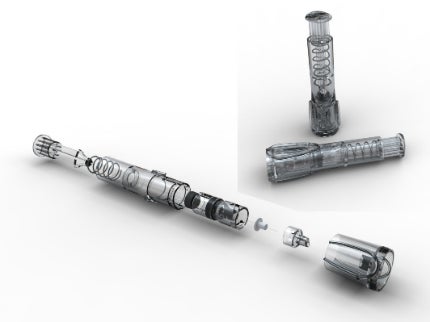
Voxdale (Antwerp, 2005) is a design, engineering and research agency for mechanical and mechatronical development of medical devices and equipment.
As a service provider and prototype producer, Voxdale is guiding projects through their initial verification and feasibility studies. Concepts and ideas are developed, product design and engineering started, risks and failure modes analysed, and functional prototypes in medical grade materials are built. Voxdale can assist in all regulatory aspects and simulate and optimise functionality, using unique finite element analysis (FEA) and computational fluid dynamics (CFD) simulation tools.
Functional prototypes used in usability and clinical trials are designed, as well as innovative industrialised solutions, tailor-made for assembly and servicing (DFA, DFS), and detailed for mass manufacturing and market introduction.
Voxdale works with GMP and ISO:13485 certified suppliers for components, materials, injection moulding, assembly and packaging.
Proof-of-concept (PoC) feasibility studies and simulations for medical devices
Based on existing or new medical research, Voxdale can initiate feasibility studies towards a first concept design of the new product. In this process, CFD and FEA simulation tools will be used to investigate, verify and optimise the functionality and proposed geometry.
These verifications can include internal and external flow analyses of liquids and gases, thermal management, and structural analysis (stress and displacement).
Medical device and equipment design: materials, engineering and computer-aided design (CAD)
The materialisation of products can start once the concept design has been established and the design input is defined. The product and system architecture will be constructed in computer-aided design (CAD) tools, materials will be chosen based on bio-compatibility, extractables and leachables, sterilisation method (i.e. gamma ray, electron beam, X-ray, ethylene oxide), and shelf-life (if applicable).
Voxdale’s materials expertise ranges from medical grade polymers (e.g. PP – Polypropylene) and elastomers (e.g. TPE), to metals (e.g. for micro needles) and composites.
If needed, external or in-house electronics and mechatronics will be integrated in the device or apparatus.
Regulatory affairs: technical files and documentation of medical devices
Parallel to the mechanical and mechatronical design, all relevant regulatory records can be composed. This comprises the initial set-up of a summary technical documentation (STED) file, failure mode and effect analysis (FMEA) on component and device level, essential requirements checklist, all according to ISO: 13485 processes and procedures.
Depending on the medical device class (e.g. I, II, III, a, b), this approach will facilitate CE-labelling and other certifications.
Prototyping: pilot batches, small series, industrialisation, manufacturing of medical devices
Voxdale has 3D printing facilities available to build prototypes to check usability, functionality, proportions and aesthetics.
In a second step, (aluminium) soft tools are built for injection moulding with approved medical grade materials and plastics to validate and use products in clinical trials (e.g. Phase I, II, III) and studies.
The resulting validation output will be implemented in a final industrialised design, to be manufactured in (steel) hard tools and moulds.
Design for assembly (DFA, e.g. for fill and finish) and design for service (DFS, if applicable) will be assessed, and bill of materials (BOM) will be released.
Packaging and packing insert (leaflet) can also be defined in this phase.
Voxdale is a member of FlandersBio.