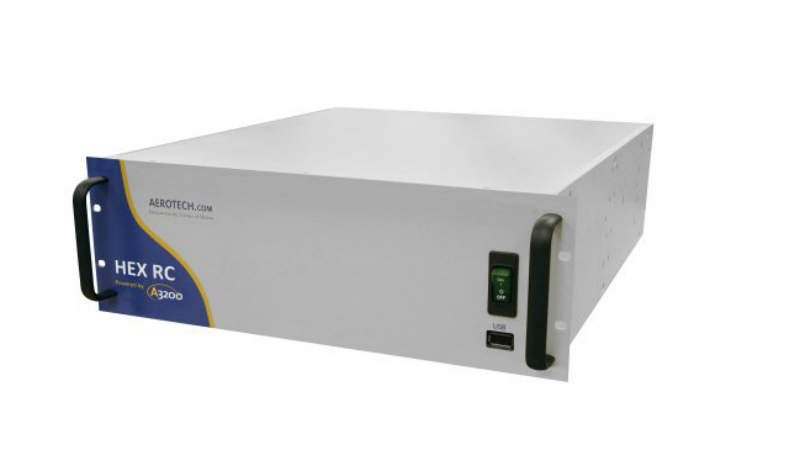
Aerotech’s HEX RC is a 6-axis motion controller ideal for controlling robotic systems such as hexapods. The HEX RC is 4U rack-mountable and compatible with the Automation 3200 (A3200) motion platform.
Key features:
- 4U high, rack-mount, six-axis controller for brush, brushless, and stepper motors
- Ideal for controlling six-axis robotic systems such as hexapods
- Real-time A3200 distributed control architecture allows synchronised motion on up to 32 axes
- FireWire® or ASCII command interface via transmission control protocol (TCP) / internet protocol (IP)
- Program in native RS-274 G-code, AeroBasic command set, C, C++/CLI, .NET, MATLAB®, or LabVIEW® for the ultimate in programming flexibility
A high-performance processor provides the intense computing power needed to run up to 32 axes, perform complex, synchronised motion trajectories, manipulate input/output (I/O), and collect data at high speeds.
Powerful control architecture
The HEX RC features six axes of drives capable of controlling any combination of brush, brushless, or stepper motors. It digitally performs both current loop and servo loop closures to ensure the highest level of positioning accuracy and performance. The HEX RC connects and controls up to 26 additional axes of servo, stepper, or piezo-driven stages using the A3200 distributed control architecture.
Interface and design options
The HEX RC is designed with an ASCII command interface over TCP/IP for control in applications such as beamlines. Alternatively, it can act as a master controller to control other A3200 external drives via the FireWire® interface.
The HEX RC accepts amplified-sine or digital encoders. Optional integrated encoder multipliers, up to X4096, ensure high-resolution positioning.
An optional six axis jog pendant permits easy, manual control of the positioning system. In safety critical applications, an emergency stop option with redundant safety relays can be added.
Flexible programming environment
Aerotech’s A3200 focuses on ease of use for the programmer, shortens development time compared with other tools, and provides the flexibility to use the tools or controller most familiar to programmers.
A complete integrated development environment and a comprehensive .NET motion library provide classes for motion, I/O, status, and diagnostic information.
You can program in Visual Studio and use the .NET library, or use the Motion Composer (IDE) to develop code with AeroBasic™ commands or G code. A LabVIEW® VI library is available for NI users, while a complete C library is available for those using Visual Basic, C++, or C.