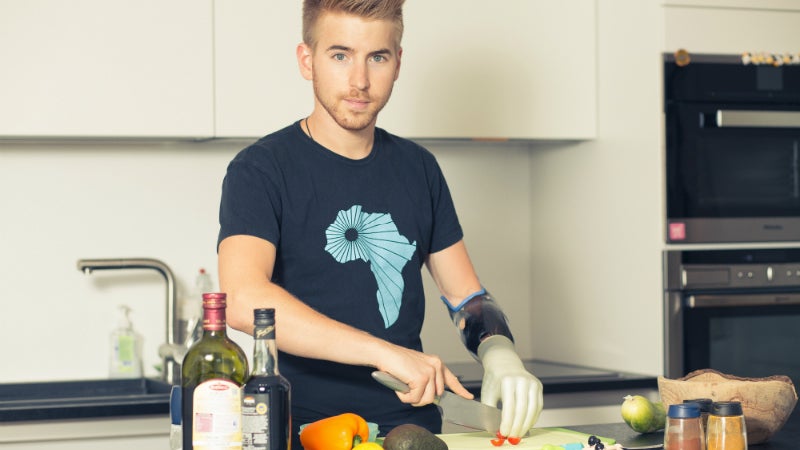
Helping return quality of life to people who have lost a hand, the Michelangelo prosthesis uses two maxon Brushless DC motors to imitate the human hand as closely as possible.
We use our hands to assemble the tiniest clockwork, to throw balls, or to communicate when language barriers are too high. This makes life very difficult for people who lose a hand in an accident, which is precisely what happened to Patrick Mayrhofer.
Patrick injured his hands so badly he chose to have his left arm amputated. Being only 20 years old at the time, he did not let this tragedy throw him off course. He said: "I am very determined and once I decide to do something, I do it."
Patrick chose to use new prosthetic hand Michelangelo, which allows him to cope with almost any situation. The prosthesis was developed by Ottobock in Vienna. It has seven types of gripping motion, which Patrick activates by contracting muscles in his arm. With the device, he is able to balance a plate on the palm of his hand, peel a banana, and take a raw egg out of a box.
In order to imitate the human hand as closely as possible, the engineers at Ottobock spent years fine-tuning the mechatronic components of the prosthesis. The components needed to be very small and light. Maxon motor developed special solutions for the prosthetic , including two Brushless DC motors.
The smaller drive has a diameter of 10mm and is used to position the thumb. The second is a larger drive responsible for the gripping movement of the fingers and thumb. This motor is fitted with a worm shaft manufactured by maxon to Ottobock’s specifications.
The swiss drive systems have to meet high-standards and operate very quietly. They are exposed to high-mechanical stress because of the gripping forces needed.
At the Cybathlon test event in the autumn of 2015, Patrick Mayrhofer out-competed the field by a wide margin.