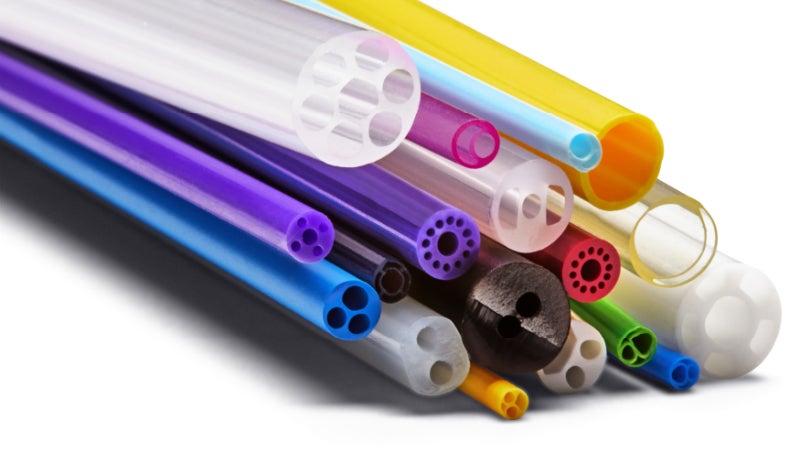
A.P. Extrusion supplies polymer tubing for the medical tubing industries, specialising in custom extrusions.
A.P. Extrusion’s tubing products range from .002in to 0.5in diameter, with tolerances as tight as +/- .00025in. With more than 30 years’ experience, A.P. Extrusion designs and manufactures solutions for the most difficult applications.
In addition, the company routinely processes research and development (R&D) prototype requests for single lumen tubing in under three weeks. Tubing types include single and multi-lumen, extremely thick or thin wall, profile extrusions, multi-layered / co-extrusions, striped, radiopaque, slit tubing, linear wire reinforced tubing, spiral tubing and solid rod monofilament extrusions.
Tubing for medical device applications
A.P. Extrusion’s primary market is the medical device industry, with applications including oxygen, air and fluid transfer; laboratory pipettes; swabs; prefilled syringe packaging; and intravenous (IV) sets. The company also has extensive experience with tubing used for medical catheters, including applications for diagnostic, guiding, electrophysiology, neuropathology, and suction catheters. A.P. Extrusion also has experience providing medical tubing for stent delivery systems and dialysis.
Custom medical tubing can be produced in clear, stock, or custom compounds and colors. A.P. Extrusion also utilizes customer specifications or supplied materials, as well as custom lengths. Additional markets include dental, pharmaceutical / laboratory, aerospace, automotive, electrical, telecom, fibre-optics, and the oil and gas energy industries.
Flexible and rigid polyvinyl (PVC) medical-grade materials for tough and flexible tubing
A.P. Extrusion has expertise using a wide array of materials including acrylonitrile butadiene styrene (ABS), Acetal, C-Flex™, ethylene-vinyl acetate (EVA), Hytrel™, and Lexan™/Polycarbonate. Unlike most manufacturers, A.P. Extrusion also specializes in flexible and rigid PVC.
Medical-grade PVC tubing is ideal for applications where tough, flexible, lightweight, and clear tubing is necessary. This tubing is extruded from nontoxic, lead-free materials, which adheres to US Food and Drug Administration (FDA) standards and is approved as a US Pharmaceutical Convention (USP) Class VI material.
Medical-grade PVC tubing is resistant to many chemicals and solvents, as well as being able to withstand repeated sterilizations. It also has a long life expectancy and can be easily bonded to plastic connectors. In non phthalate (DEHP) plasticizer grades, it can be used for applications involving high-risk patients.
Other materials A.P Extrusion uses include Nylon 11,12 & 6/6, Pebax™, Polyethylene, Polypropylene, Polysulfone, Santoprene™, Surlyn™, Texin™, thermoplastic elastomers (TPE), thermoplastic polyurethane (TPU), Ultem™, and Urethanes.
High-quality and precise tubing manufacturing, with rapid turnaround
A.P. Extrusion’s manufacturing process starts with the design of extrusion tooling. The company utilizes SolidWorks Flow Simulation and computer-aided design (CAD), alongside an in-house machine shop to ensure high-quality and rapid turnaround.
Once the designs reach the manufacturing floor, A.P Extrusions ensures dimensional accuracy and repeatability with real-time process monitoring using continuous laser scanning of tubing diameter for all extrusions and ultrasonic wall thickness measurement for critical parts. In-process quality control is performed using the Micro-Vu system and all extrusion lines maintain statistical process control (SPC) data to ensure stability. The facility is ISO:9001-2008 certified.
Post-extrusion production operations include precision-cut lengths, spiral cutting, heat ageing, and custom packaging for ultraviolet (UV) protection. Contact A.P Extrusion using the enquiry form for specialized customer requirements.
About A.P. Extrusion and its excellent customer service
Located in Salem, New Hampshire, A.P. Extrusion benefits from the outstanding high-tech educational system and workforce of the greater Boston area. The company maintains strong partnerships with local universities, which offer polymer engineering programs.
A.P. Extrusion has long-term relationships with raw material and compounding suppliers. The company routinely offers lead times under three weeks for single lumen tubing using standard materials and four to six weeks for custom designs and materials (depending upon complexity and volume). In addition, A.P Extrusion maintains >95% on-time delivery and work directly with customers to meet their unique needs.