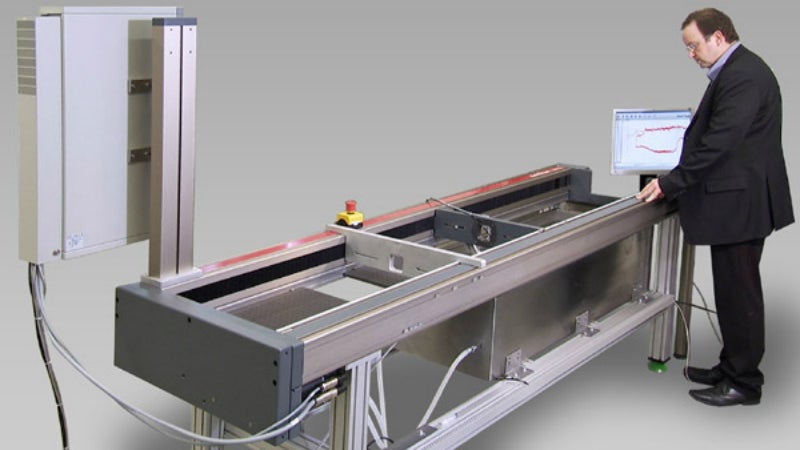
Recent worldwide demands in the booming medical sector have resulted in the growth of more complex materials and component testing.
Increasing regulations regarding certification, traceability and auditing of data have introduced additional challenges to laboratory process management. As a result, more and more companies are turning to Zwick to provide a complete solution, due to its experience in the industry (which spans many decades).
Complex materials and component testing solutions
Zwick’s medical industry coordinator, Mr Erik Berndt, pays close attention to the market needs including the introduction of new products, applications and customer support. “Unlike many products in the market, complex mechanical tests, particularly those in orthopaedics, require a close co-operation between materials testing experts and medical specialists in order to match the test conditions as closely as possible to those found in the human body,” he explains.
Horizontal material-testing machine
“In addition, Zwick has recently worked with many global organisations that develop products for cardiovascular surgery. They need to measure the forces experienced when surgeons insert catheters into the human body to carry out investigations and surgery,” Mr Berndt continues.
“After we understood the test requirements, we realised that the normal materials testing machine, which sits on a laboratory bench, was not a good solution, so we developed a special horizontal version. To this point, we have sold more than ten of these systems worldwide.
“A key topic for many of our customers is the FDA certification, which is concerned with the traceability of data. This is often not included in typical materials testing software, but is managed by using third party add-on packages. Yet Zwick’s expanded traceability option, meeting FDA 21 CFR part 11, is fully integrated into its testXpert® II modular software and offers a complete audit trail on the data managed and produced by the software.”
Single-source data management
Mr Berndt also stated: “Part of this system is the user administration, enabling laboratory managers to have total flexibility in setting access rights. All activities are then logged, and customers benefit from a single source, easy-to-implement solution for their data management. In addition, all software version updates are automatically integrated, thereby saving expensive re-audit costs.”
DQ / IQ / OQ Support
Erik Berndt adds that “our customers often need DQ / IQ / OQ support. This ensures and documents that the testing system has been correctly installed and operates precisely according to the specification. As a consultancy option, Zwick’s installation engineers are trained to install, commission, and provide the DQ / IQ / OQ documentation for the complete testing system.”
About the Zwick Roell Group
Zwick Roell Group customers benefit from more than 150 years of experience in the manufacturing of high quality testing systems. Zwick is the global leader in static testing and is experiencing significant growth with its dynamic test systems. A financially strong and family-run business, its innovative product developments, diverse product range and global support provide tailored solutions targeted specifically at the needs of both research and development, and quality assurance customers.
Serving more than 20 industry sectors with 950 employees, via manufacturing facilities in Germany, regional headquarters in Atlanta, Georgia, USA and Singapore, as well as offices in 56 countries worldwide, the brand name Zwick is a guarantee of the highest quality and support. For more information see our website.