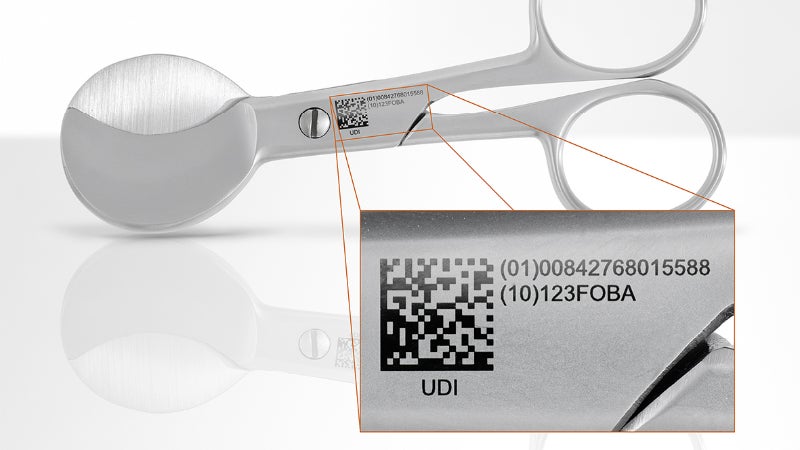
With the second international Patient Safety Day taking place in September, FOBA and MedicalMountains highlight their contributions with laser marking.
As well as the patients themselves, medical and health care professionals are challenged to implement adequate measures and standards to reduce treatment risks. Manufacturers also contribute to patient safety by producing low-risk medical devices. Reliable traceability of these devices for safety reasons depends significantly on direct part marking (DPM).
Patient Safety Day aims to increase public awareness. Organised by the Aktionsbündnis Patientensicherheit and supported by the German Federal Ministry of Health, the focus of this year is on medication safety. Hospitals, nursing homes, and other health organisations are invited to participate, as well as manufacturers and consultants.
FOBA’s laser marking and engraving is part of MedicalMountains, a cluster initiative with over 200 member companies, which represents quality and innovation in medical technology. FOBA’s high-performing machines form an important part of the production lines of medical device manufacturers worldwide.
Chairwoman of MedicalMountains Yvonne Glienke explains: "Patients’ safety is every medical company’s final concern.
"For that reason we offer training and information seminars on related subjects such as CE marking, biocompatibility, technical documentation, and the European medical device regulation.
"All implemented measures’ target is to ensure patients benefit from safe products and services."
Latest changes in the European medical device regulations will be subject of a training offered by "MedicalMountains" in Q1 2017, providing help and information for management to adapt necessary changes in businesses.
Extended official directives such as Unique Device Identification (UDI) regulations by the Food and Drug Association (FDA) or the European Medical Device Regulation (MDR) are intended to better control the big variety of products on the medical market, to store information in a central data base and protect quality standards. Not only products of low-risk such as dressing material or stethoscopes are affected, but also middle-to-high-risk devices such as hearing aids, medical tubes, intravenous catheters, scalpels, or implants.
DPM on medical devices ensures continuous traceability from manufacturer to patient and is mandatory for many industries. MedicalMountains provides support for its member companies to find adequate marking technologies.
Laser marking appears to be a highly reliable technique for medical devices, which requires biocompatible and hygienic marks. High-marking quality with long-term resistance ensures traceability throughout the whole product life cycle. In terms of medical implants for example, these marks contain data on time and place of production, further processing, attending physicians, time and place of surgery, and patient data. All information can be taken directly from the product and transferred further into hospital and other documentation systems.
Manufacturers benefit from FOBA’s Holistic Enhanced Laser Process (HELP), a vision-based marking system. This verifies parts and marking contents before, during, and after marking. An efficient production can therefore be guaranteed and production costs can be reduced by up to 80%.
Laser marking is most suitable for DPM on materials such as titanium and other metals or different plastics. Also highly sensitive silicone products can be adequately marked by FOBA UV-lasers or the pulsed Ytterbium fiber-lasers from the FOBA Y-Series.
The flexible vision-based FOBA marking systems solve the current demands of medical device manufacturers for industrial parts marking.