
If you have a medical device that’s performing well, the temptation can be to sit tight – as the old adage goes, ‘if it ain’t broke, don’t fix it’. However, no device can dominate the market forever, and many older devices may need an update to stay competitive.
“Medical devices are a complex beast – the years taken to develop them and the high price tag of that R&D are reflective of their life-saving nature. Unfortunately, as is so often said, all good things must, and do, come to an end,” says Tom Ackrill, business development manager at medical contract manufacturer ITL Group.
How well do you really know your competitors?
Access the most comprehensive Company Profiles on the market, powered by GlobalData. Save hours of research. Gain competitive edge.
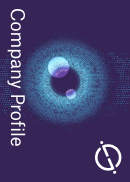
Thank you!
Your download email will arrive shortly
Not ready to buy yet? Download a free sample
We are confident about the unique quality of our Company Profiles. However, we want you to make the most beneficial decision for your business, so we offer a free sample that you can download by submitting the below form
By GlobalDataIf the medical device is quite simple, this ‘end’ may come in the form of patent expiry, which opens the floodgates to a slew of competitors. That’s great news if you’re a rival manufacturer, but can pose challenges if the product is yours.
In a recent case study, Carl Savage of New Jersey-based contract manufacturer MICRO discussed how his company was tasked with re-engineering a wound closure device coming off patent. In order to forestall imitators, the device needed to be redesigned and its price point cut in half.
“Designing a product to look and perform equivalently to its predecessor without sacrificing integrity and functionality can be challenging,” said Savage. “Surgeons are accustomed to an instrument performing a certain way for a specific procedure. An updated design needs to be able to accomplish the same function, fit, and form as its predecessor.”
In this case, the team was able to re-evaluate the manufacturing and assembly process and make cost savings in key areas. When the device did go off patent, the OEM was better placed to fend off competitors.
When parts can’t be procured
That said, medical devices tend to be protected by multiple patents, rather than just one. And while a pharmaceutical product coming off patent is immediately at risk from generics, that isn’t the case in med tech. Right from the outset, a rival manufacturer would usually be able to build a similar product without infringing your intellectual property.
The real issue for ageing medical devices isn’t so much a patent cliff as component obsolescence, in which one or more of the essential parts become impossible to source. As Ackrill explains, obsolescence can strike at any point in the product life cycle.
“Usually it’s more common in older legacy devices that have been kept on the market long past their intended design life,” he says. “As technology moves on, manufacturers of those individual components change their range, and develop something new, faster, smaller, better. The legacy components start to fall by the wayside.”
This applies above all to electronics – a fast-evolving field in which components have very short lifecycles. Unlike the consumer electronics market, which thrives on rapid change and new product lines, the average medical device will be on the market for ten years or more. In other words, the product and technology lifecycles are misaligned.
According to the manufacturing services company Jabil, one in five healthcare device manufacturers struggle with component shortages and, even where the legacy technology is still available, suppliers can’t always meet original equipment manufacturer (OEM) demand.
“To the layman, a simple unavailability of a component isn’t a big deal – it’s a case of finding something else that can do the same job, and substituting it in,” says Ackrill. “Unfortunately, the medical device regulatory landscape of the 21st century is extremely risk-centric, and changing even the simplest of components within a device has to be done and documented in a way that demonstrates to the world that your product is still safe.”
Finding solutions
According to Ackrill, a good manufacturing company (be that the OEM or a contractor) would be able to keep an eye on the availability of components, and stock up as soon as they become hard to find. Companies may even invest in special humidity chambers for sensitive electronics, enabling them to store the components as long as needed.
However, there will come a point where the legacy technology no longer exists and the product needs to be redesigned. If the manufacturer is lucky, a suitable alternative with the same form, fit and function will already exist on the market, keeping disruption to a minimum. Or an alternative will exist with slightly different parameters – a common situation with older products.
“ITL has dealt with situations where a component that was used previously on a printed circuit board (PCB) was of a through-hole type, but the modern alternative is in a surface mount package type,” says Ackill. “This gives a situation where the component does the same job, but can’t be fitted in the same way.”
He adds that manufacturers could take a couple of approaches here, each with distinct advantages and disadvantages. The first, which is more drastic, is to re-lay the printed circuit board to accommodate the new componentry.
“The second is that the new component can be fitted onto a ‘daughter board’,” he says. “Essentially this is a miniature PCB that houses just one individual component, which then plugs in to the existing space on the board, in the same way that Brits might use a travel adaptor on a mains plug when we visit the US or the EU.”
A square peg in a round hole
Unfortunately, there are also situations in which no substitute exists. You might have an analogue component that has been superseded by a digital one, or a component that has been physically reshaped.
“A square peg trying to fit into a round hole is an appropriate analogy,” says Ackrill. “While a good engineering team can undertake activities to figure out how to make the square peg fit, the risk level from a regulatory point of view is much higher. The onus is on proving there is absolutely no impact on the performance of the device in any way, shape or form, and this needs to be a collaborative effort between the legal manufacturer and the design team.”
He points out that, while the challenges are not insurmountable in most cases, it’s important to have an R&D team on board who are au fait with the device requirements and the wider manufacturing environment.
It also pays to be aware of these problems well ahead of time. Many successful med tech companies take the approach of incremental product improvement – redesigning the product in stages, rather than facing the financial blow of component obsolescence.
“Component obsolescence is seen as a bit of a bogeyman in the industry because of the knock-on effects of a simple component change when it comes to maintaining compliance,” says Ackrill. “Luckily there are companies out there, such as the ITL Group, that are often asked to come to the rescue of a product heading towards the medical device graveyard.”