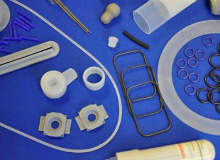
Parylene is an advanced soft polymer conformal coating which produces an ultra thin, pinhole free finish ideally suited for medical products and implantable devices as it offers protection against the effects of fluids and solvents, while maintaining its lubricity and flexibility.
Parylene is applied at room temperature by a vapour deposition process. The monomer condenses and polymerizes on the component’s surface in a polycrystalline formation providing high conformance to the typography of the substrate whether, metal, elastomer or plastic. The benefits of Parylene include:
- Ultra thin transparent bio compatible protection
- Highly lubricious dry film lubricant
- Outstanding chemical, moisture and electrical barrier protection
- Conforms precisely to contours with deep crevice penetration
Everlube® products
We have a wide range of bespoke and branded Everlube® solid film lubricant coatings used to protect components from temperature, corrosion and chemical attack, these can also be applied to improve the lubricity and release properties of materials. Dry film lubricants are often used when liquid lubricants such as grease and oils cannot be used as they will remain intact and provide continuous lubrication.
Surface pre-treatment is also essential to achieve the optimum finish and we have advanced facilities which can provide treatments for a range of components.
Contolled shot peening
Failure of metallic devices i.e. implants can often be attributed to stress corrosion cracking and fatigue caused by the flexing and movement of critical parts. These failures mechanisms are also common in major industries such as aerospace, automotive, energy and power generation.
A proven solution to this problem is the application of controlled shot peening to replace the harmful residual stresses caused during manufacture or use with beneficial compressive stresses which prevent the initiation of cracks in the surface of the component. This is a highly controlled process used as part of the manufacturing supply chain for major OEM’s and can be easily adapted for any size of component.
Peentex finishing
The Peentex process is applied by Controlled Shot Peening to create a finish that can be both decorative and practical and can be applied to metal, glass, wood and acrylic sheeting. Controlled Shot Peening has been successfully used as part of the supply chain in major industries associated with the engineered surface finishing of metals, including steels, stainless steels, aluminium, titanium and copper alloys to improve wear and resistance to corrosion.
When Peentex is applied this substantially improves the wear and scratch resistance characteristics of the surface material. It is heavily used in the architectural market for railings, wall cladding and signage. The surface produced also gives a finish which diffuses direct light and glare, which minimises the effect of fingerprints and mild blemishes and makes it resistant to written graffiti and stickers.
We applied the Peentex process to provide a decorative finish and protect the base sections of The Spire in Dublin, Ireland and was also used in the refurbishment of King’s Cross Station in London.