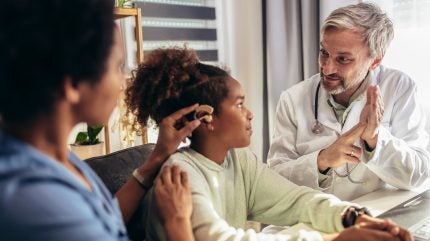
As populations age and the proportion of hearing-impaired people rises, GlobalData forecasts that the hearing implants market will grow to reach $2.83bn by 2030, up from $2.08bn today. Innovations have greatly increased the range of options available for the surgical treatment of hearing loss and are key to industry growth.
Cochlear implants currently dominate the market, but bone-anchored hearing implants, middle ear implants, and auditory brainstem implants (ABI) are also predicted to grow in market value over the coming decade.
A stable regulatory landscape leaves plenty of room for further innovation, including in hearables for health monitoring, but key components need to be reliable and achieve high performance. Notably, the tiny system of wires that make hearing aids work needs precision in the manufacturing process. For growth to continue at pace, expert partners in manufacturing are required.
The difficulties in hearing aid manufacturing
There can be considerable complexities in manufacturing hearing aids. “Wire sizes for the array wire [in hearing implants] can be below 20 microns,” explains Gene Kleinschmit, global product manager for medical wire at leading alloy and materials innovator Alleima. “It is hard to see and hard to feel in your hand, but the operators must carefully handle the wire when they are setting up the machines to draw the wire to size and apply coatings to the wire.”
Specialist manufacturers can help medical device companies overcome these challenges and push the envelope with new hearing aid designs.
“Recent advancements have been in smaller diameter wires that allow the entire device to be reduced in size and also allow for the addition of more wires to the array to improve the quality of hearing,” explains Kleinschmit. “The next major advance will be to move the external speech processor to the implanted portion of the device. When this occurs there will be no external device that can be seen, so no one will know that a person is using the device.”
Additionally, the use of hearables for health monitoring is another growing industry trend set to fuel demand for tiny wire components. These in-ear devices use sensors to monitor health and could reach a market size of $131bn by 2030, according to GlobalData. Most hearables include a microphone and sensors that can measure variables from heart rate viability (HRV) to breathing and digestion. Once again, precision in manufacturing these devices will be paramount for their long-term viability.
Specialists in components for hearing implants
Alleima is a world-leading manufacturer of advanced stainless steels, special alloys, and heating systems for various industries. The company’s high-grade fine wires and wire-based components are already widely used in cochlear implants, pacemaker leads, and glucose monitors.
Allemia’s expertise is vital in meeting the demand for reliable wire transmitters, which are essential to the manufacture of cochlear implants and other hearing aids. Working closely with customers to understand the operational parameters of each device, Alleima offers an individualised service that can advise on the best materials, customisation, and coating requirements for new medical device projects.
To learn more about Alleima and the current state of the hearing aids market, download this specially commissioned whitepaper.