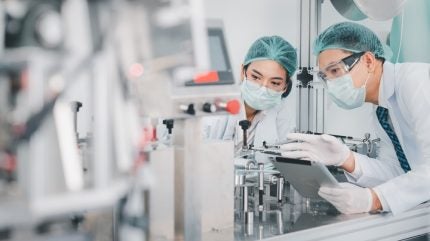
Uses of new technologies are having a significant influence on the development of medical devices. If utilised correctly, development timelines can be reduced, and devices can enter the market more quickly to achieve cash flow.
In the development space, few technologies are enabling greater possibilities than 3D printing. This high-tech manufacturing tool can dramatically reduce timeframes and allow greater levels of individualisation with devices to meet the exact needs of patients.
“3D printing has been extensively adopted by the medical industry with applications including surgical planning, by providing a physical model of the operation area; training; and orthotics and prosthetics, among others. This adoption rate is due to this method’s quick turnaround compared to the traditional methods,” explains Emma Sturdee, associate analyst for GlobalData
“Major benefits of 3D printing include customization, lower costs, speed of production, and waste reduction. Due to these advantages, companies are investing more in their 3D printing technology and even forming partnerships with other companies in the 3D printing space.”
Another key market trend is patient monitoring devices, which are becoming more common and increase the treatment possibilities for patients. Wearable device uses are growing in monitoring health levels. At the same time, the rise of smart implants such as pacemakers is expanding the possibilities for gathering precise data from within the body – with the right coating essential for the performance of such devices.
“The patient monitoring market will experience tremendous expansion,” adds Sturdee. “Several factors are driving the growth of the patient monitoring market such as ageing populations, technological advancements, the increasing adoption of telehealth, and the demand for home monitoring. There has also been an increase in regulatory support.”
The vital role of coatings in reducing development timelines for medical devices
While technology can help to reduce the development timelines for a medical device, so too can the right coating. However, with increasing specialist requirements for advanced devices, selecting the optimal coating requires the knowledge of industry specialists.
Formacoat is one such specialist that is establishing itself as the go-to solutions provider for medical device coatings. Based in Minnesota, the family-run company offers expert guidance on the right coating to meet the exact needs of specific medical devices, stocking a diverse range of around 100 coatings from more than 40 trusted vendors.
The company has also been using 3D printing within its highly innovative R&D department. The team can start to determine the optimum coating based on the technical drawings – before the device may even have been completed. Such technologies allow coatings for complex geometries or niche materials to be figured out well in advance and avoid delays later down the development timeline.
“If they have this device, or they want to see coatings, we can take all that information and do it in one quick shot – just two to four weeks. Boom, boom, boom. We’re done, and we’re on with the coating, then moving on to the next phases. We can really help them validate the coating process,” explained Todd Paulsen, vice-president of Formacoat in a recent webinar hosted by GlobalData.
“We can give customers all the opportunities, everything right off the bat. We take a look at what we’ve got, work out what works best for the customers, and we put them back in the driver’s seat with their development,” added Paulsen. “That in itself is a huge time saving – an average of six months off a design process.”
For further market analysis of the medical devices and to learn more about the work of Formacoat, view the on-demand version of the recent webinar – titled How a Diverse Coating Selection Can Help Accelerate Development of Medical Devices – enter your details on this link.